Katzhagen modeling department
The Holcim cement container type SWB made by GOFA - a construction report
After finishing both of the RhB Sb depressed-center freight cars, a suitable freight was missing...
I couldn't stand it - the cement container used by Holcim was a must. The container is made by a German company called GOFA, which expands to Gocher Fahrzeugbau. This roughly translates to "Goch vehicle construction". Goch is a small town in Germany near the Dutch border.
I was able to start the project on the 16th of December, 2010, after most of the ordered materials had arrived...
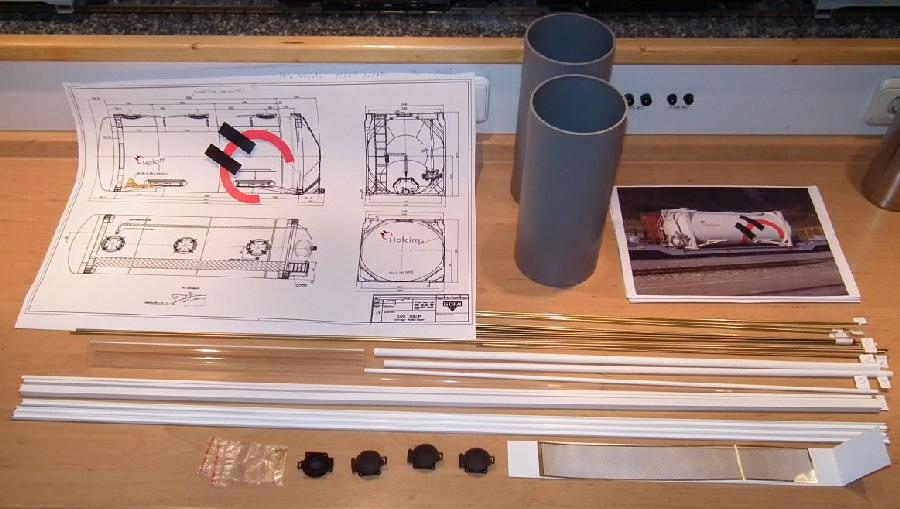
Doesn't look that terrible - but it's hard to imagine that this collection of brass and plastic is meant to become a cement container...
I started with a 110mm waste pipe for the tank which I had fetched from a DIY shop before.
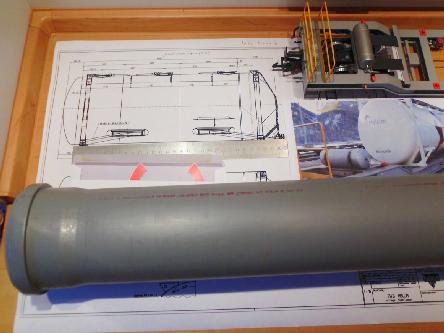
Prototype drawing and pictures, 110mm waste pipe for the tank.
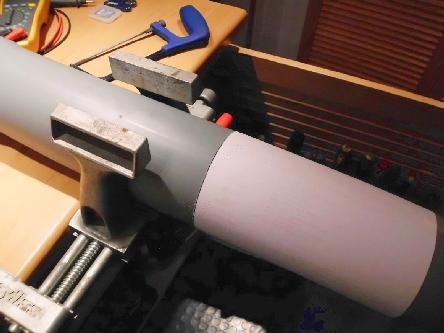
Sawing off segments of the pipe to length using a paper collar.
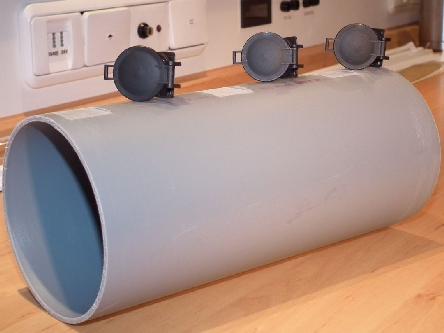
Fitting in the dome covers - the waste pipe is really tenacious...
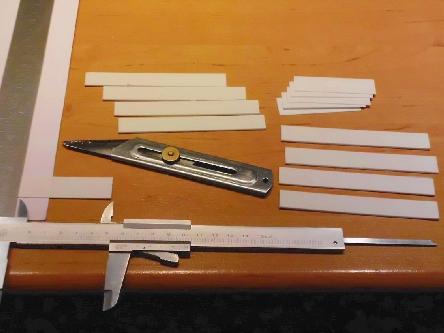
Cutting the vessel's supports to length.
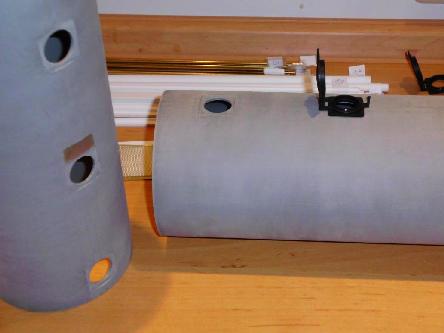
The pipes were sanded for varnishing before mounting the small parts.
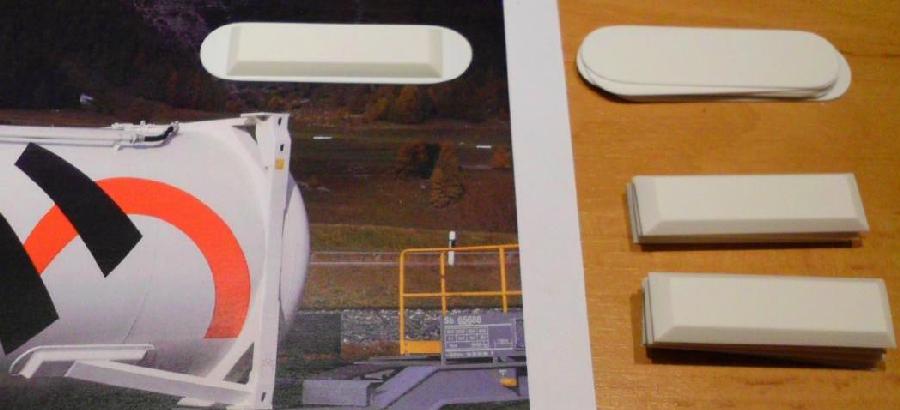
Parts for the vessel's side supports - made from several layers of 0.5 mm and 1.5 mm polystyrene plates. And some patience for sanding it...
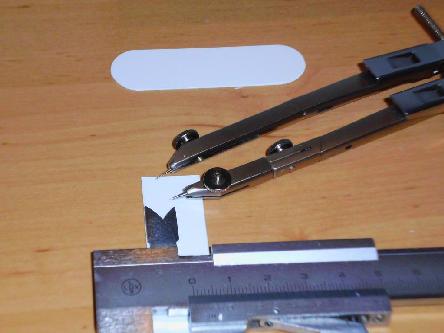
A pair of compasses helps to get the rounding right...
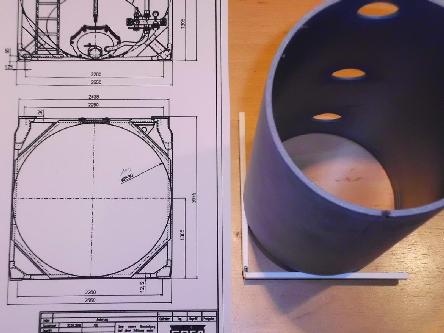
First steps for building the frames using 8x4mm square tubing.
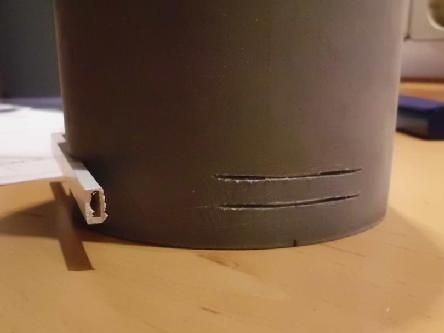
Applying cuts to the cylinder and fitting in the square tubing.
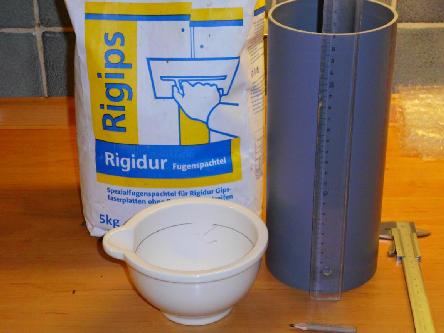
A mortar as a mould for the hemisphere - a die for swaging !
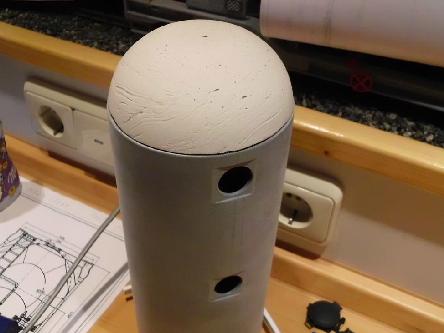
Fits ! Just a little filling and sanding...
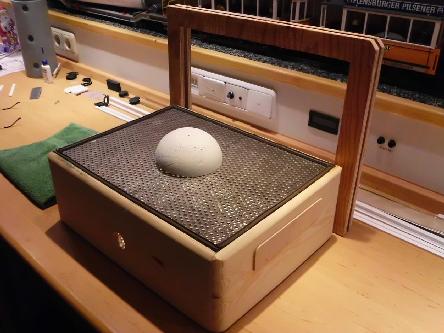
A wooden box, a perforated plate and a vacuum cleaner...
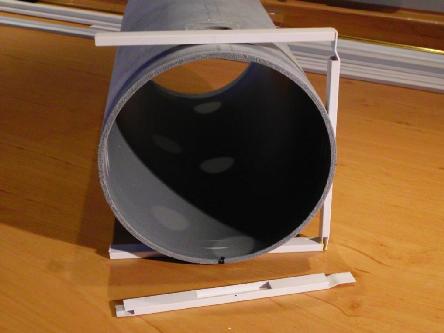
In the meantime some work was done with the frame's construction...
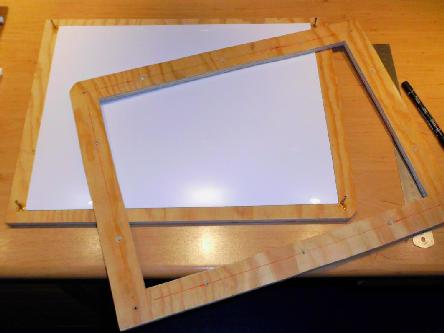
After getting hold of 1.0mm acrylonitrile butadiene styrene (ABS) plates...
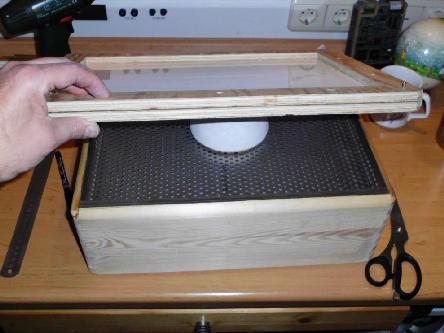
... a plate was mounted inside a wooden frame (so that it wouldn't move)
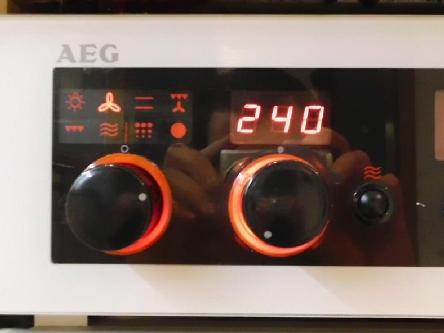
Heating up the stove to 240 C (464 F).
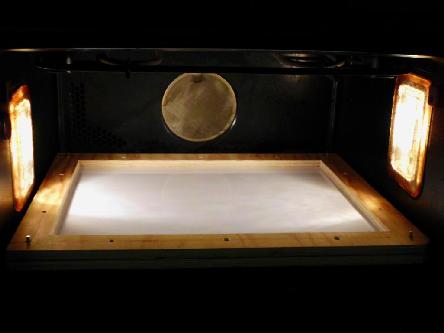
Baking plastic - two minutes are enough.
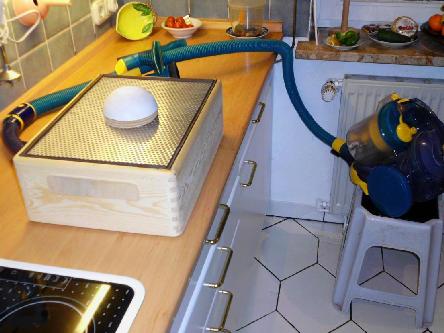
Last checks of the equipment while baking the ABS...
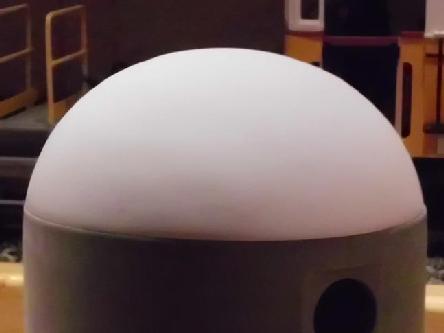
Quod demonstrandum erat ! The result confirms theory.
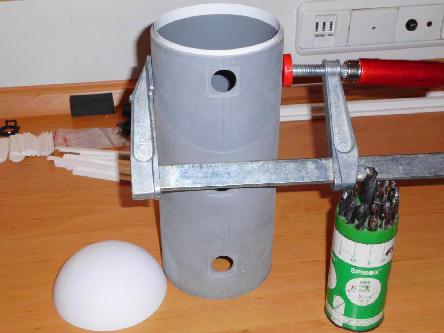
A little pressure improves the pipe's roundness... bonding is up next then.
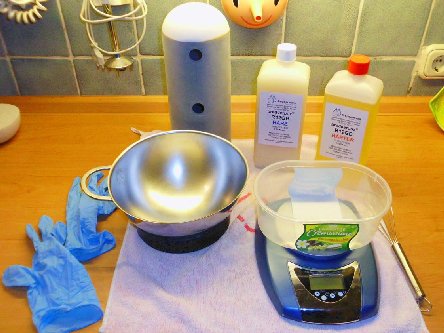
Breaking new ground again - preparations for casting polyurethane resin.
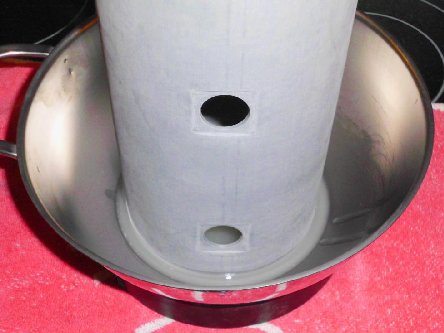
And now it's waiting to see if it works as expected...
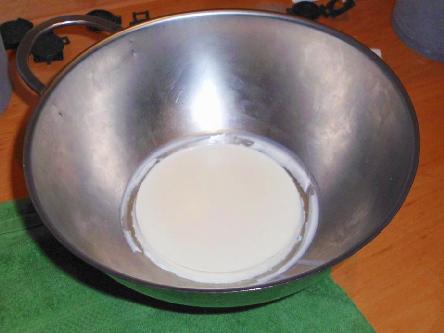
The casting was OK - but the mould didn't cooperate...
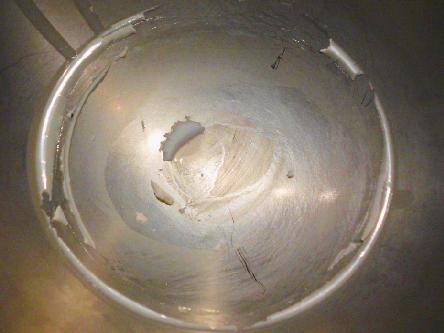
Kneading the mould did the trick to free the result.
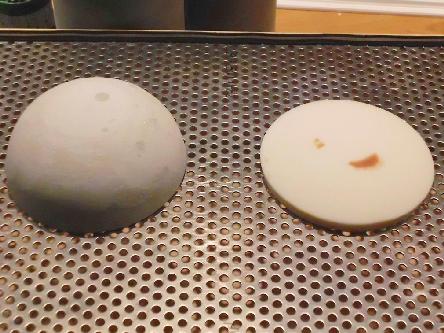
Swaging again - a hemisphere (drywall adhesive) and flat rounding (resin).
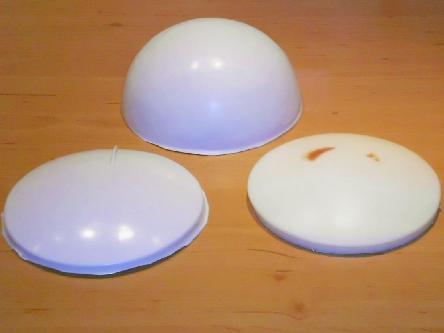
Reproducible results.
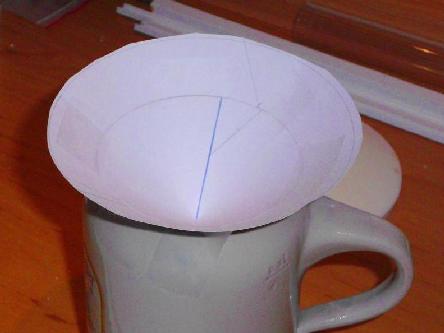
After some brooding, an idea and playing with Pi...
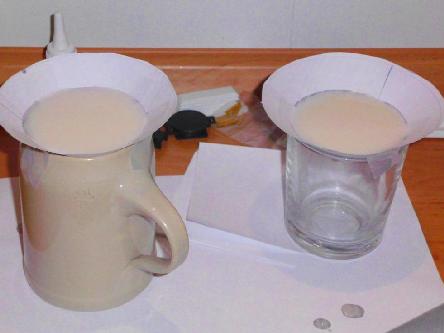
...moulds were made for swaging further parts.
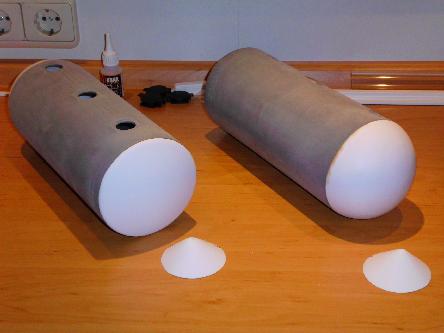
I was really afraid of the hemisphere and its cone - until I got this result.
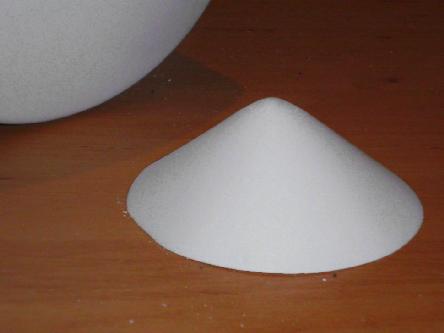
Swaged part - its mould was made from paper mounted inside a glass.
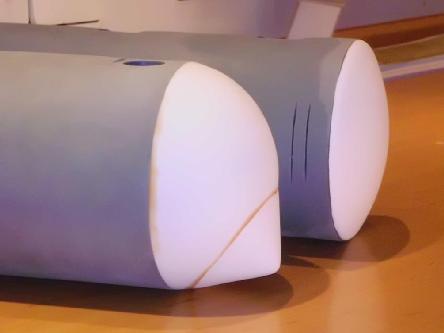
The vessels' basic form is finished - after a lot of sanding.
Annotation to swaging: ABS of 1.0mm seems to be the best choice for this purpose. 1.5mm plates cause much more ado after swaging, more difficult to cut, more sanding required - and swaging itself is not as smooth as with the 1.0mm plates. I suspect that 0.5mm plates might be not robust enough for swaging - but this is a vague guess only.
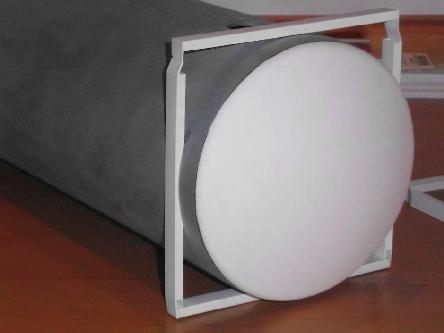
Just little progress today - the rear side's outer frame assmebly.
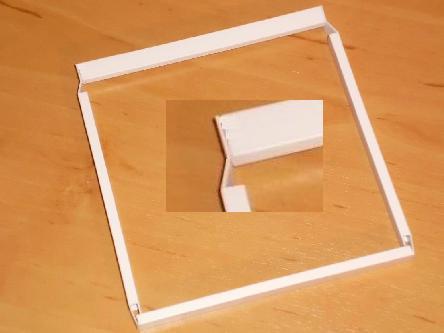
The front side's outer frame which isn't intergrated into the vessel's body.
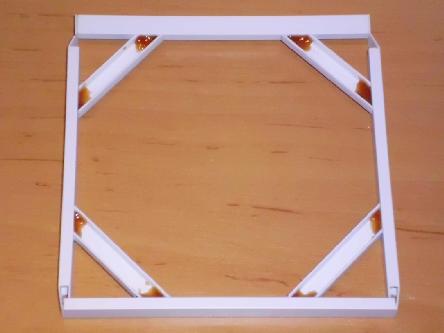
Reinforcement of the front frame's edges using a methacrylic glue.
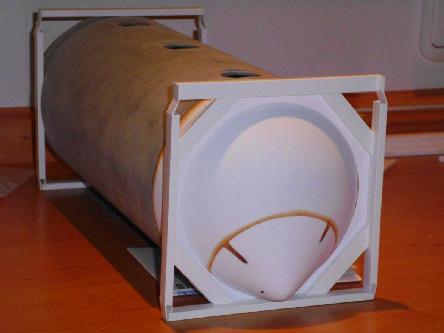
Front frame with tank support plate.
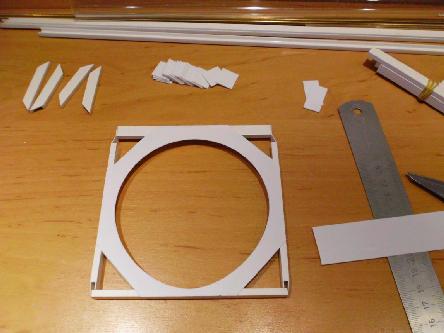
More small parts required than expected - no boredom !
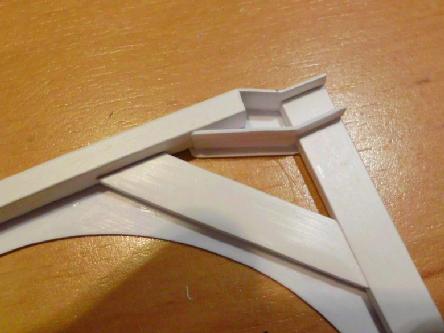
The front frame consists of approx. 30 parts - if I were a machine...
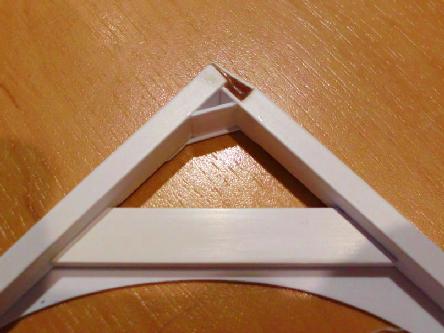
It's the same with the rear frame - structural fortification.
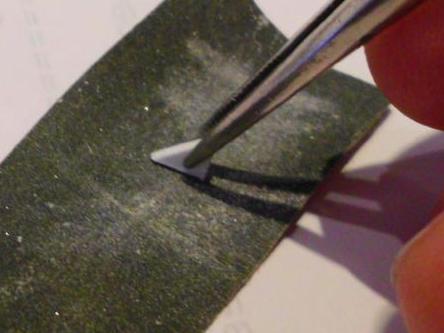
Sanding with a pair of tweezers - I never had to do THIS before.
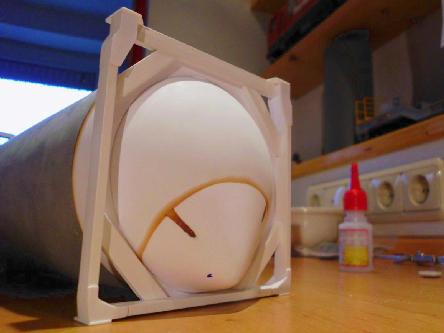
The front frame seems to fit...
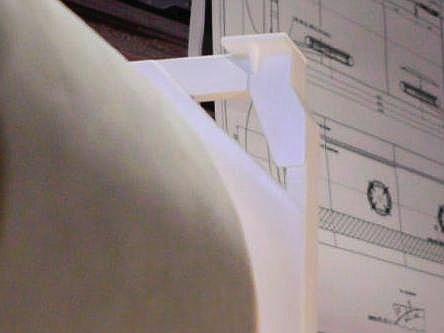
and the same seems to be valid for the rear one.
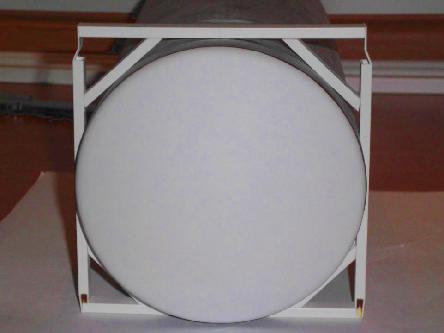
Mounting the diagonal braces on the rear frame.
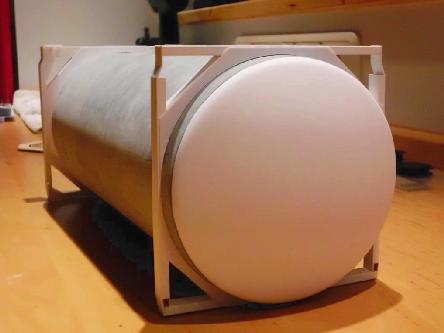
The rear frame after panelling the braces.
For some reason I hadn't expected the frames to be that complicated.
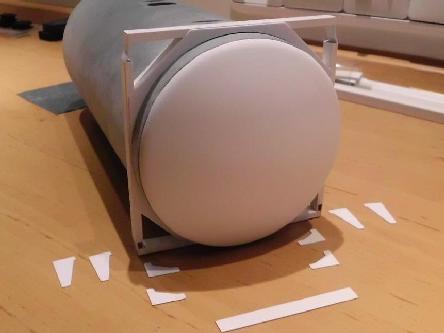
Further work on the rear frame
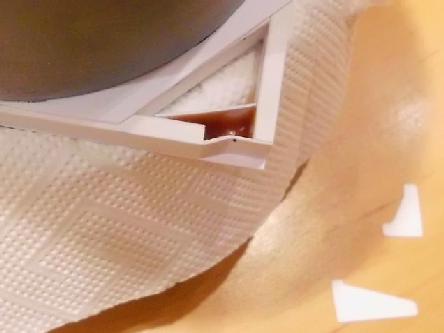
Again methacrylic glue is used as a fortification for the structure.
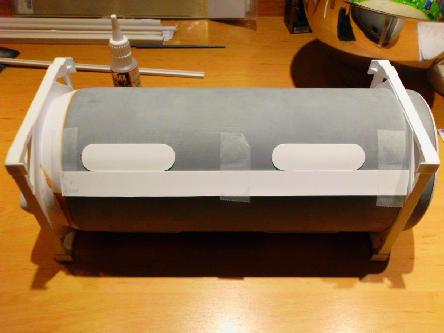
Mounting the supporting braces is done with the help of a simple template.
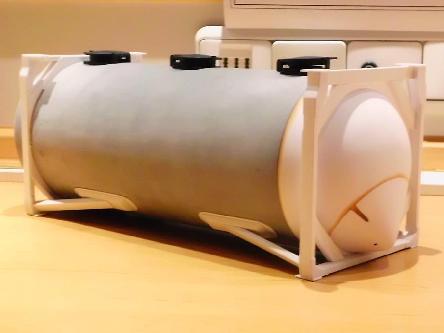
The vessel's completed frame structure.
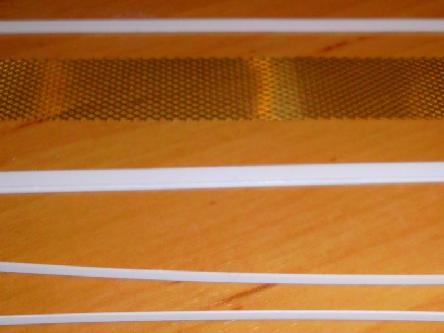
The walkway's frame is made from two layers.
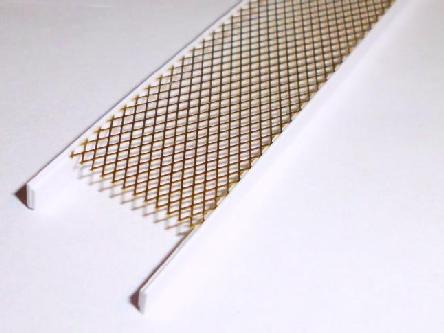
Perforated plate placed inside the frame.
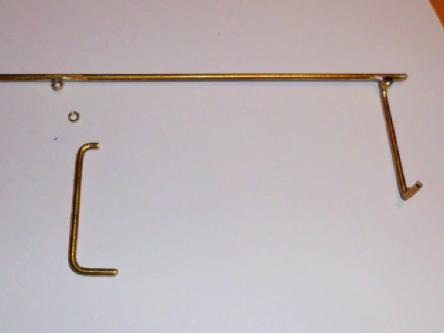
The handrail is made from brass.
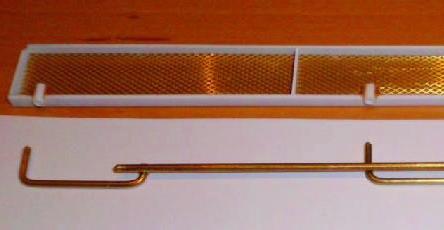
With the bearings on the frame, the handrail and its braces become tiltable.
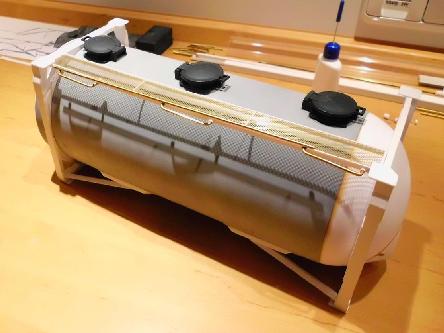
Quite OK for a first impression.
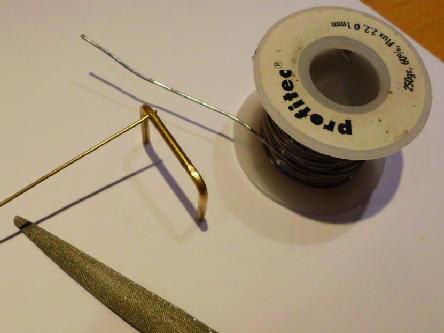
Some soldering on the ladder's frame.
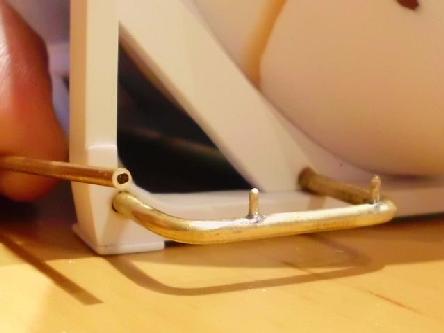
Frame holding the ladder.
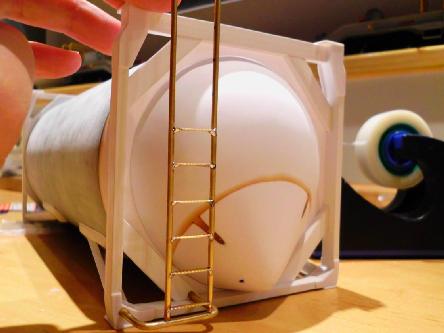
The ladder will be mounted after varnishing - therefore the construction.
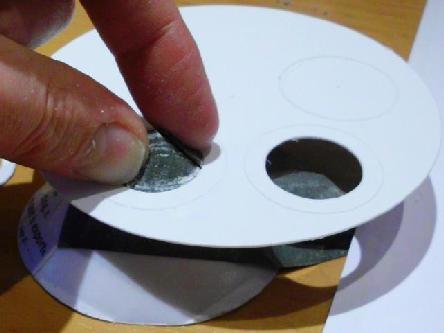
Grinding the cone into the flange of the pump sump.
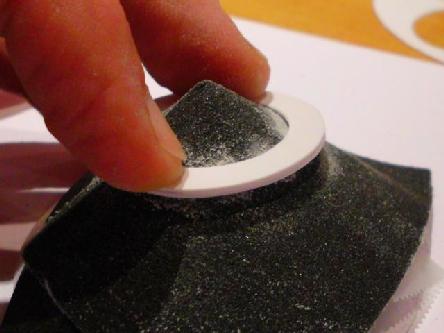
Grinding the cone into the three layers of 0.5mm ABS plates.
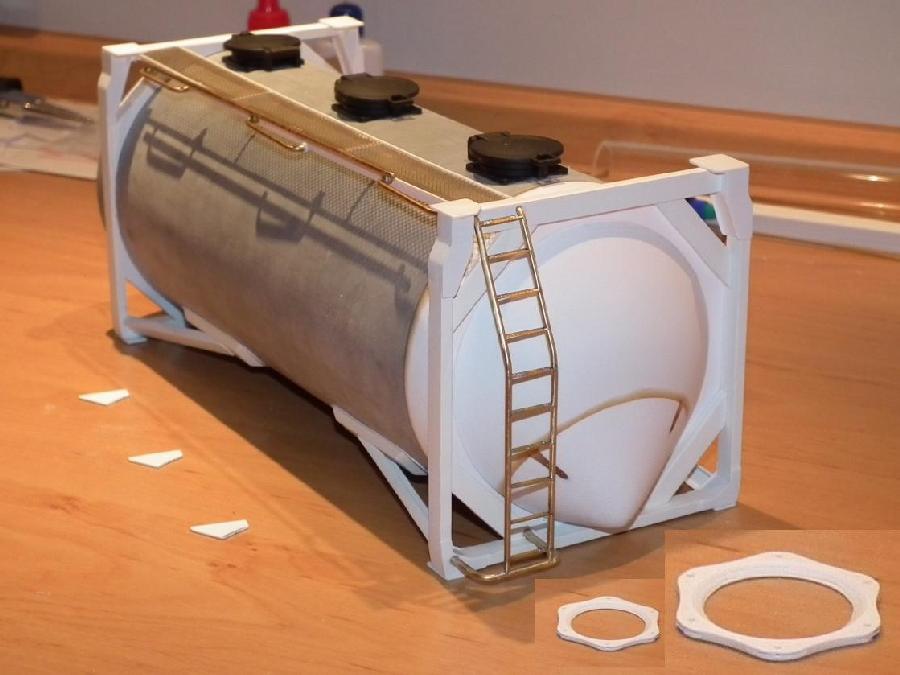
The flange of the pump sump cover was a real challenge. The walkway's supports (three small parts on the left will be mounted later, after varnishing.
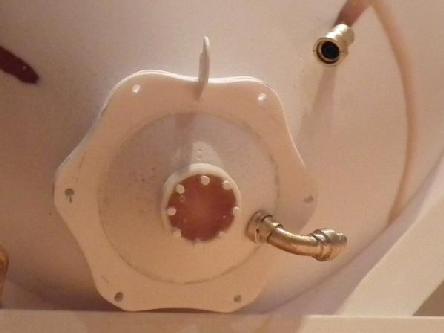
Pump sump flange after mounting and hose fittings.
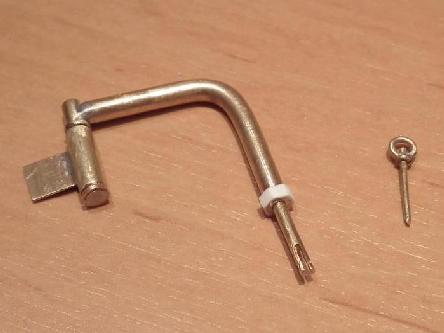
Swivel arm and eyebolt (1 of 6) for the pump sump cover
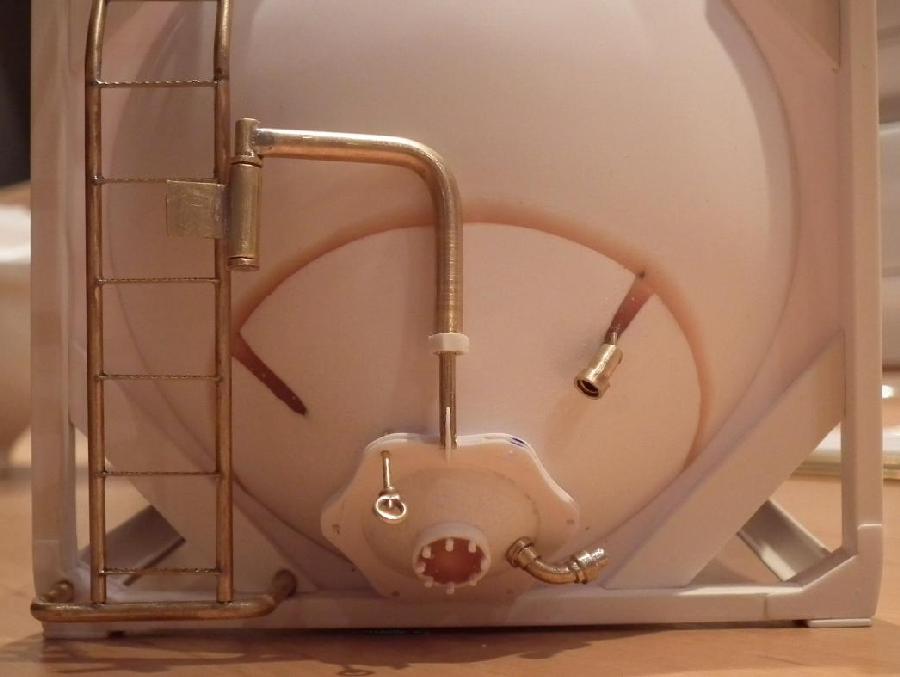
Swivel arm and eyebolt seem to fit. The swivel arm's mounting plate will be fastened in the vessel's body and the eyebolts will be cut to length after varnishing.
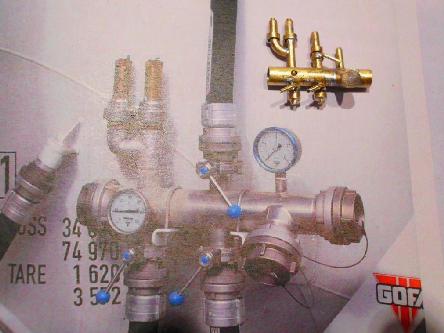
Plumbing work - Fitting for filling and unloading the tank.
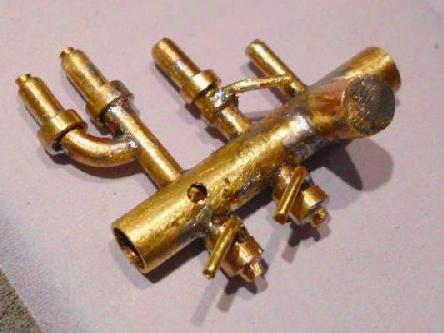
The fitting is made from brass rods and pipes of different diameters.
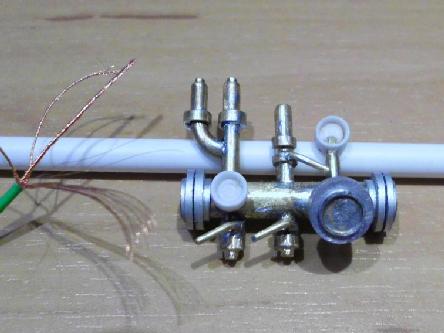
After adding the flange covers made from aluminum and the instruments...
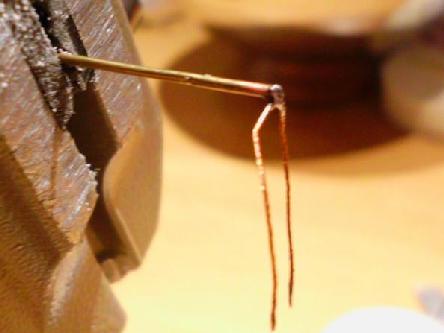
... the story with the wire ropes for the flange covers had to be solved.
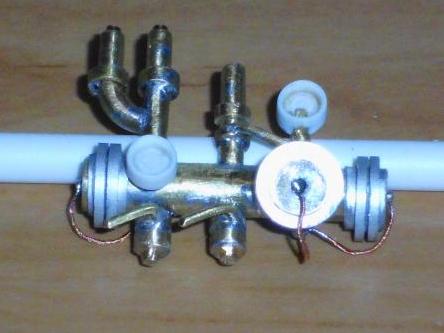
The wire ropes were made from fibres of a 0.35mm Lifycy data cable.
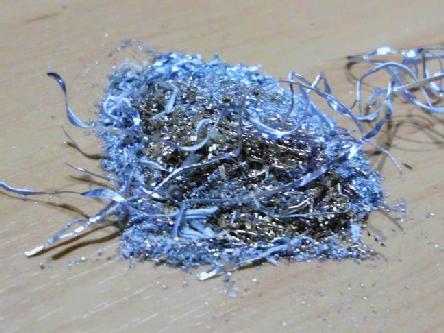
Such a little fitting (not even 3cm wide !) and so many filings...
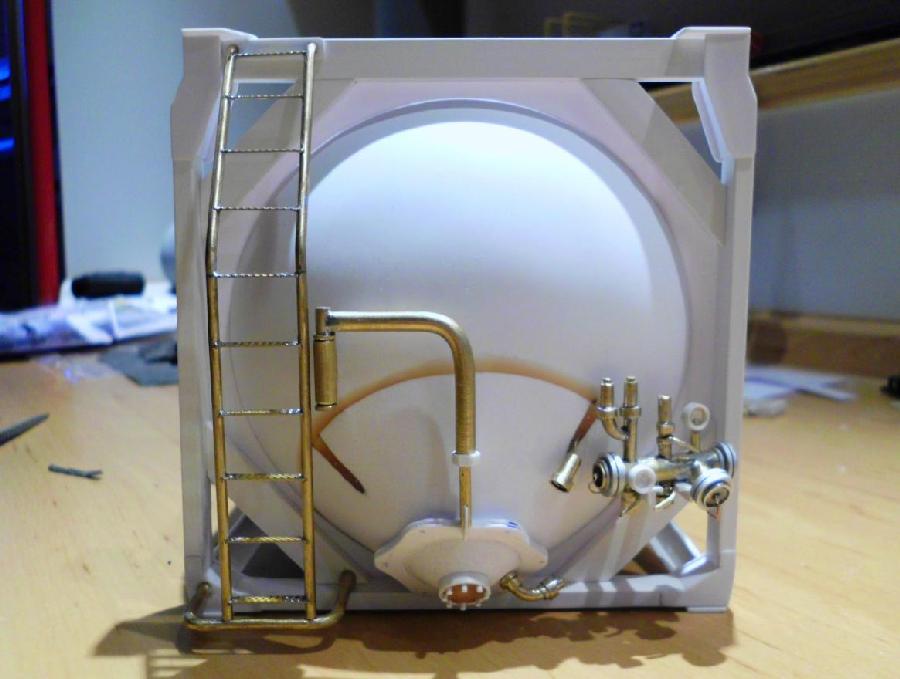
The fitting ready to be varnished with the meanwhile mounted swivel arm.
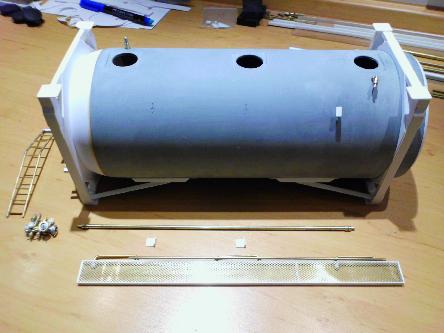
Well.... just a few pipes and holders left...
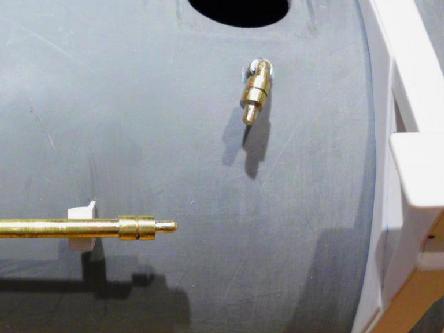
There are no bent pipes - just hoses.
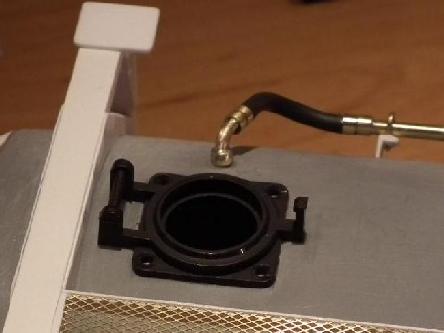
An example for a hose's usage.
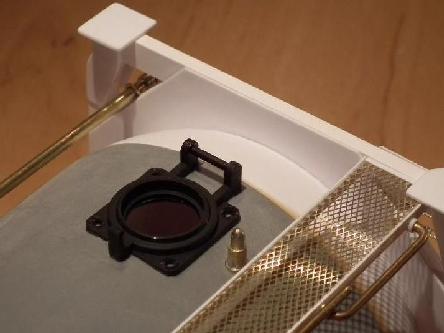
Details - walkway with handrail, dome covers, ventilation and charging pipe.
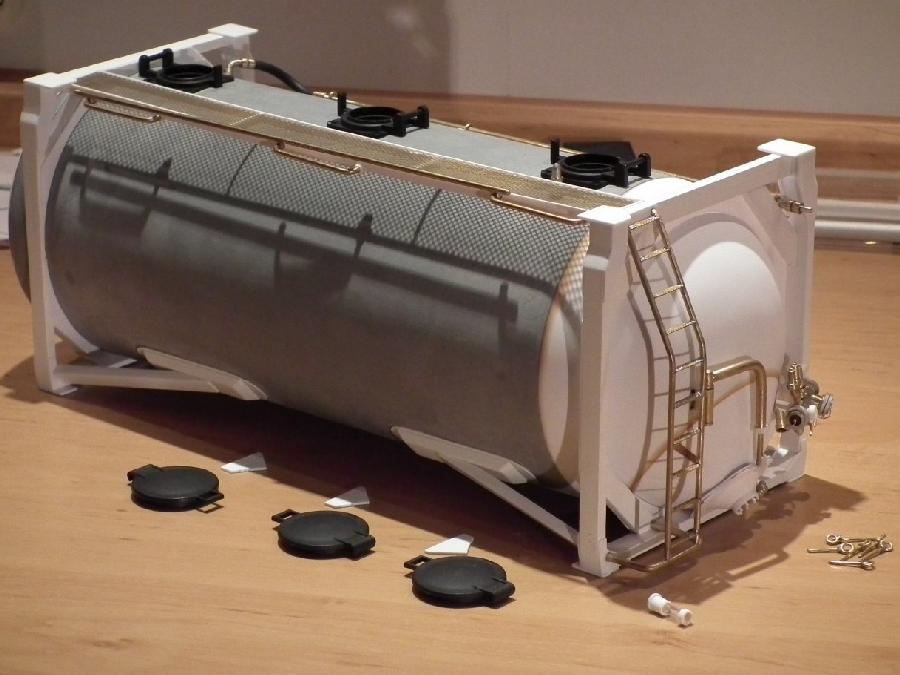
Now just a single detail is missing...
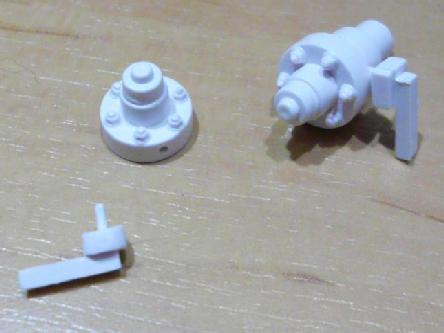
... i.e. the discharging pipe and its butterfly valve.
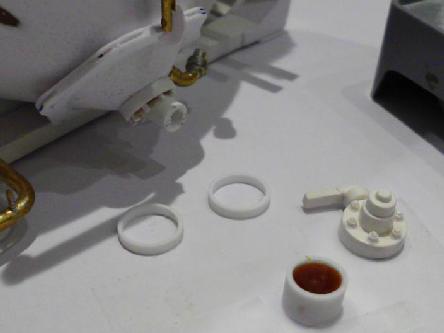
A flange and a cover are also required.
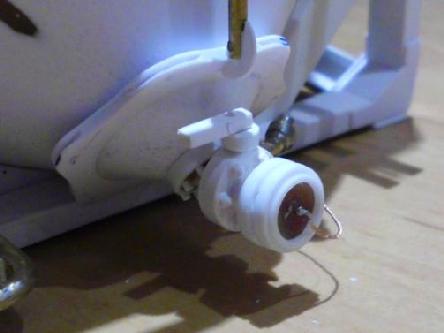
Made from the functionless valve of a small LGB tank car.
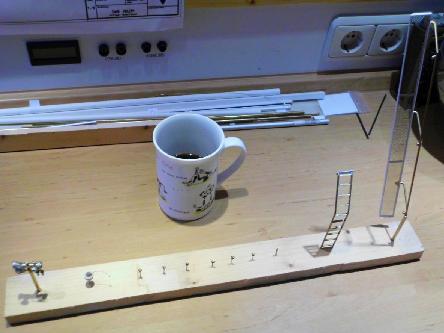
Simple appliance for varnishing the parts which won't be white.
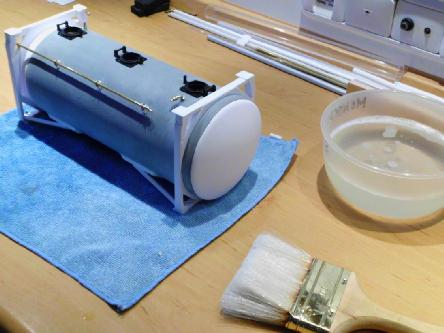
Removal of dust and grease before applying the paint.
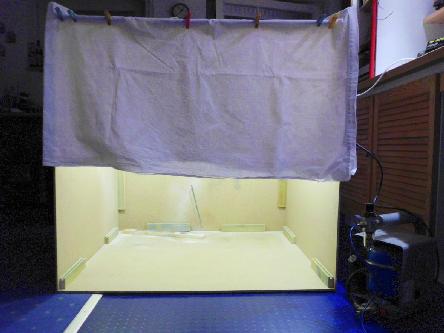
Simple paint cabin - five chipboards are set up in less than 10 minutes.
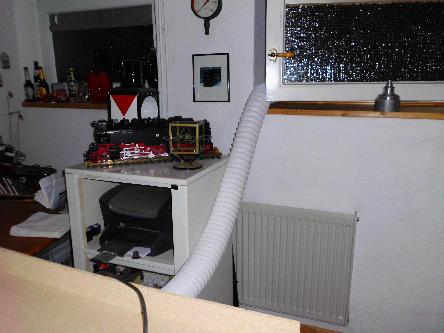
An old computer fan and a hose...
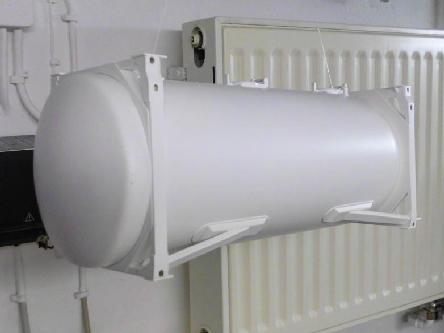
Drying the paint...
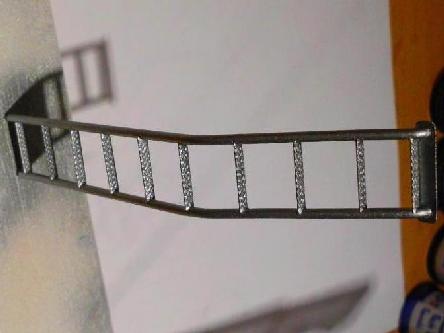
Silvered...
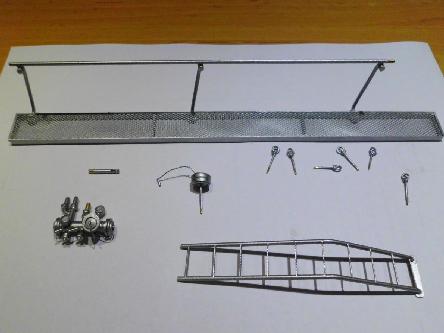
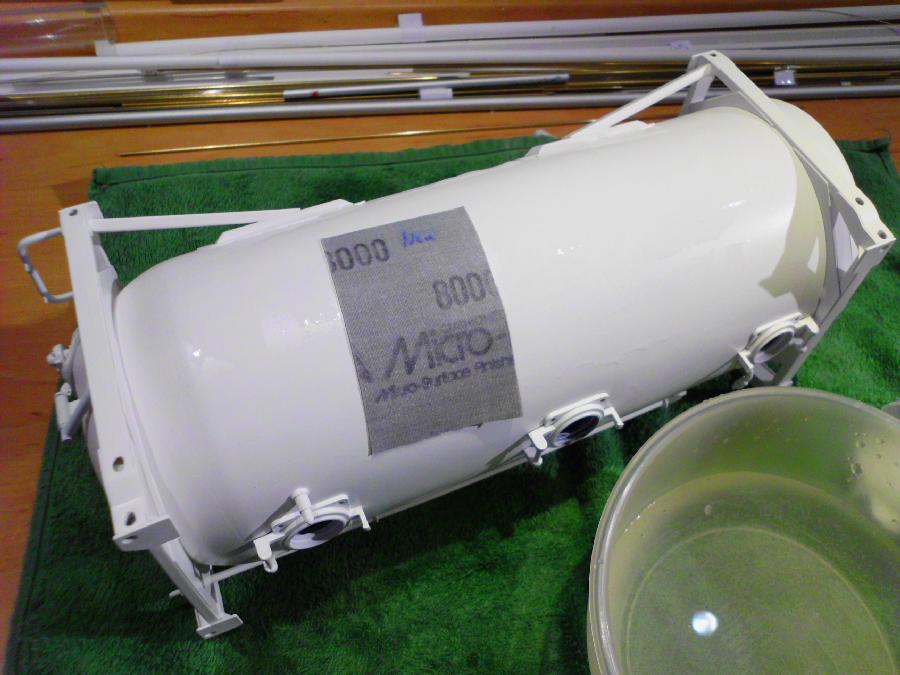
Sanding again right after applying the paint ?! Sanding wet with a grid of 3200 and 8000 (usually used for acrylic glass) - for the decals.
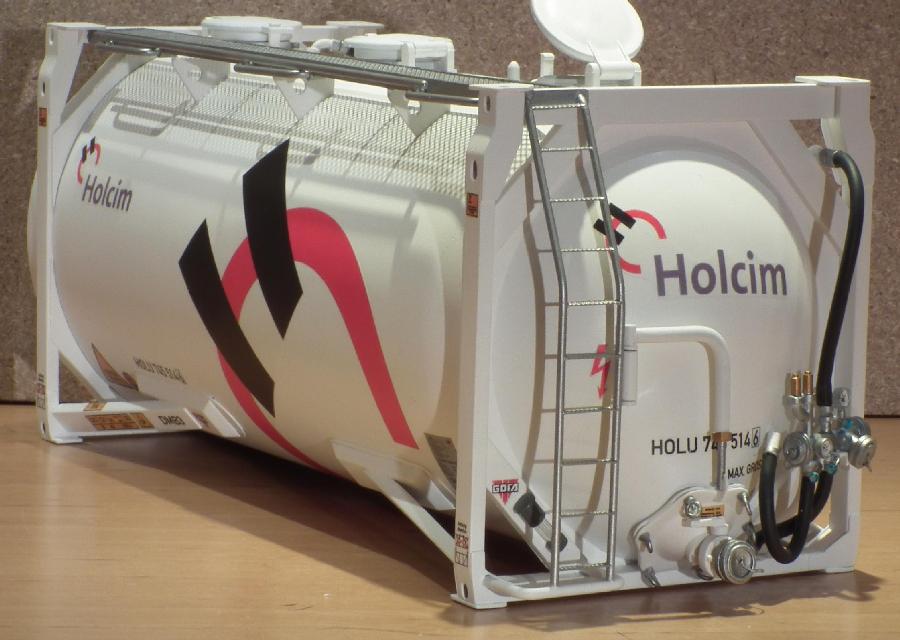
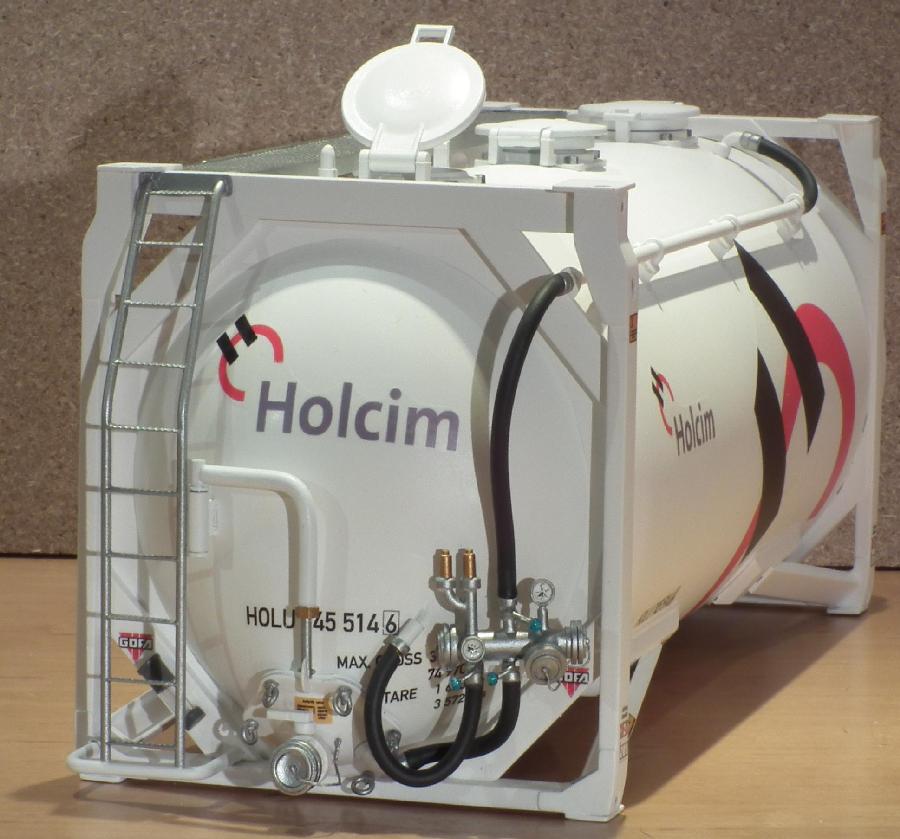
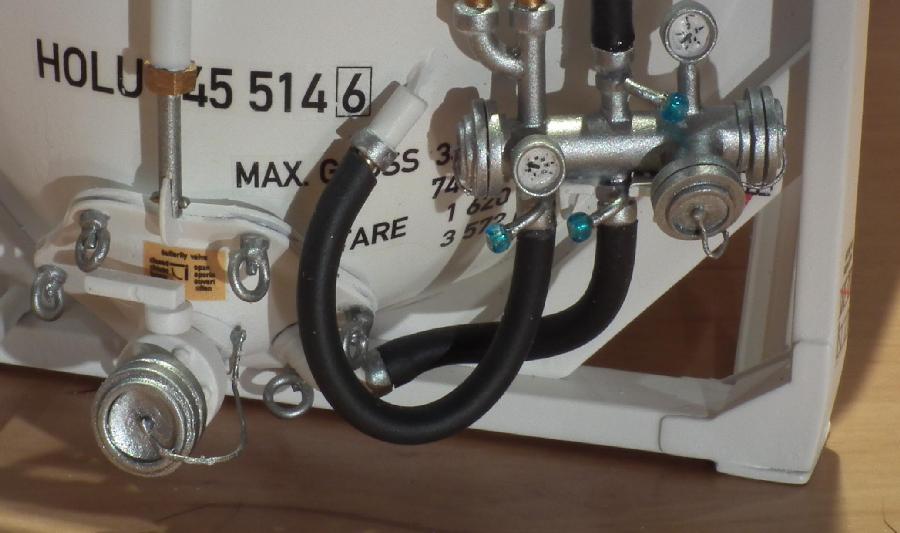
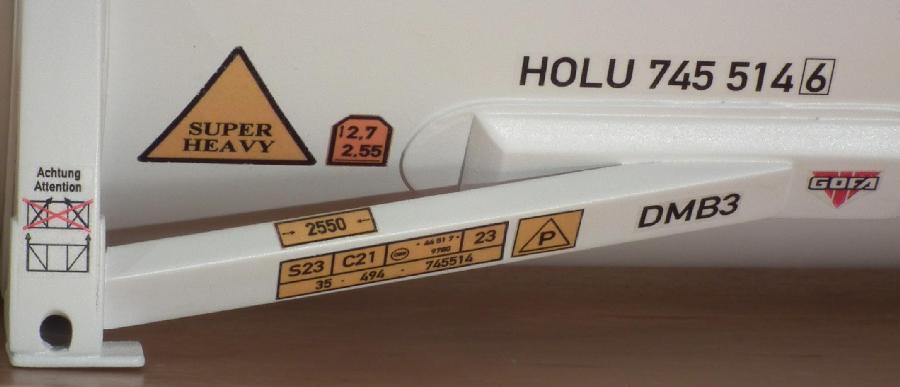
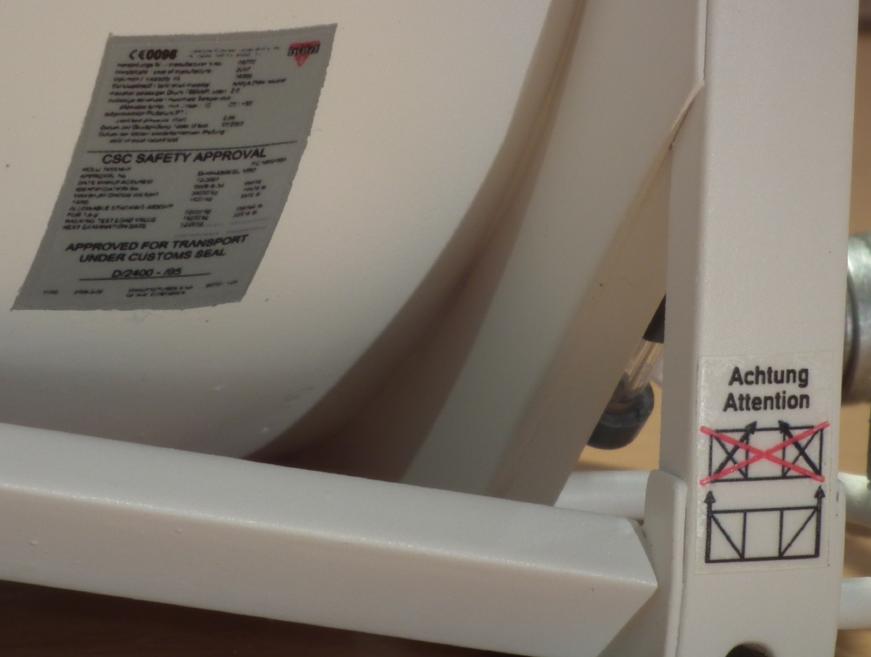
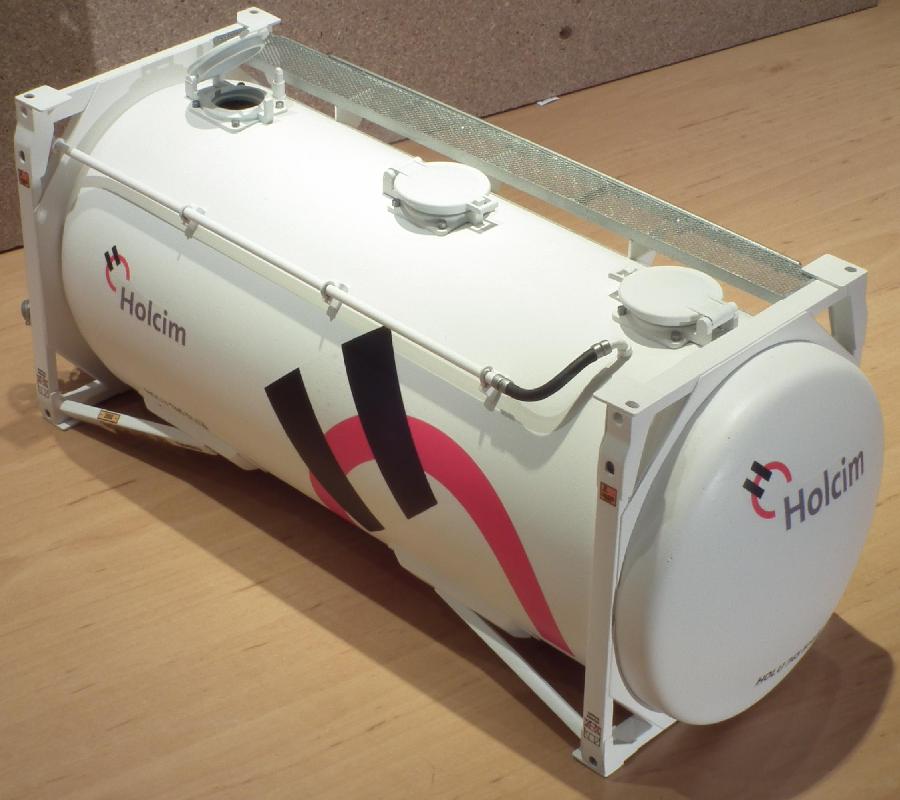
And this is the purpose - freight for the Sb
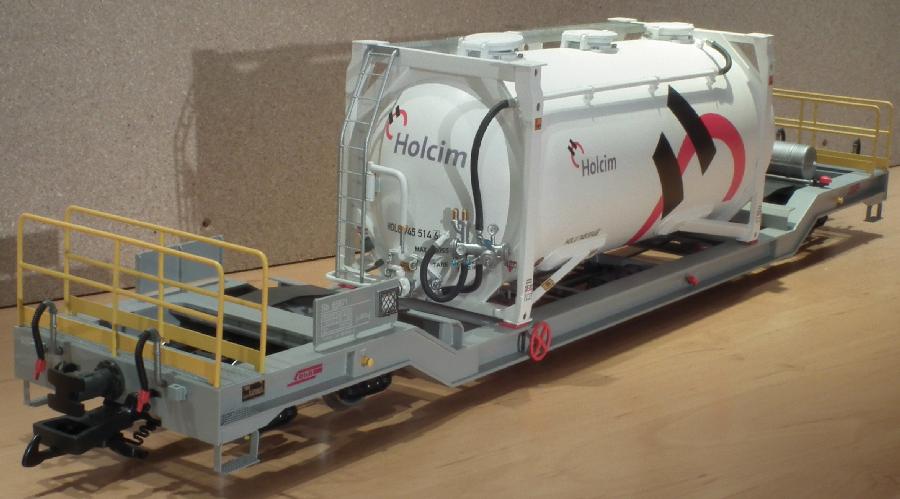
In case you feel like building one of these beauties yourself, it's no problem to provide a drawing, prototype pictures and the lettering for private purposes.