Katzhagen modeling department
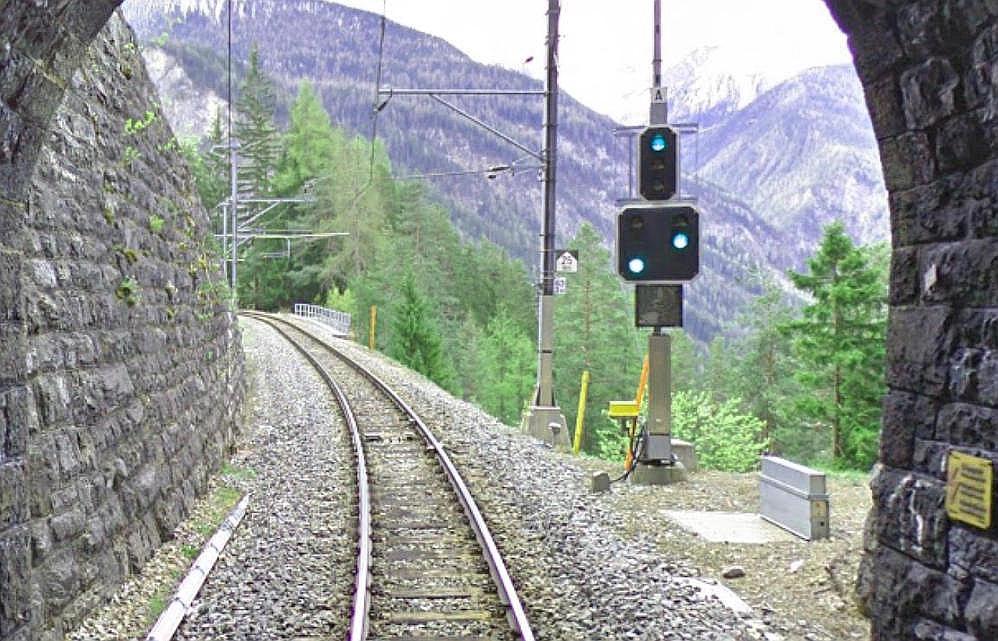
Rhaetian Railways model signals made from brass
had been on the list for quite some time as a replacement for the more or less simple two-aspect signals offered by LGB in order to accomplish more prototypical scenarios along the tracks. Unfortunately, this wish had been thwarted by the manufacturers so far by either closing their business or by uncooperative behaviour regarding the disclosure of their products' details. Hence building these signals myself was the only way - which turned out to be a partially bumpy road.
Basic research
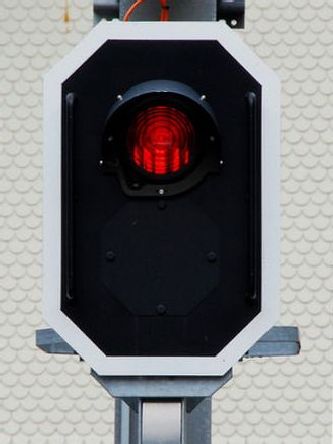
Strange single-aspect prototype in Berguen
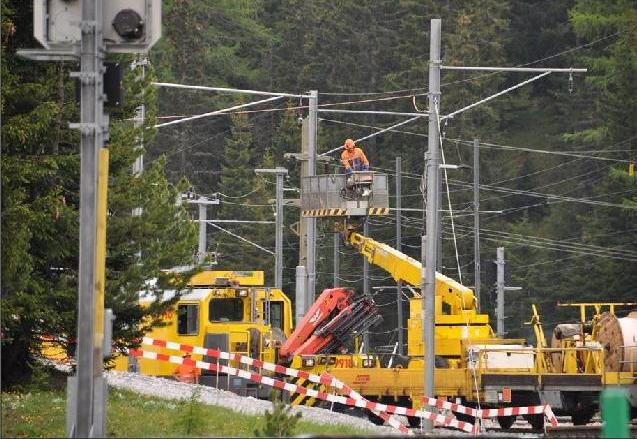
Research result: There are many different kinds of signal masts around at the RhB - things simply are in flux.
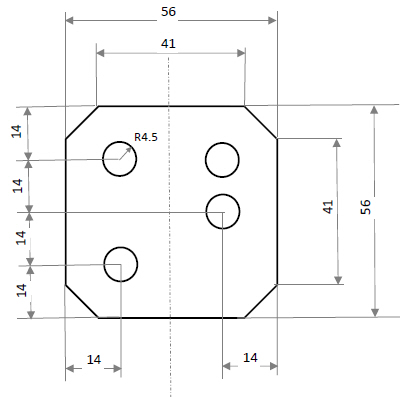
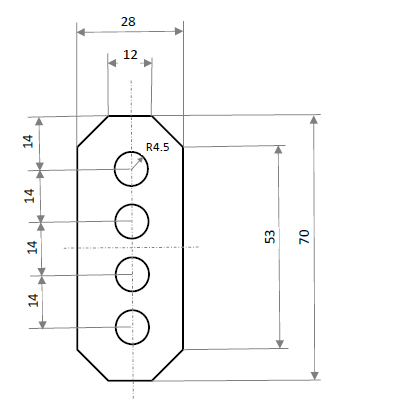
The minor challenge with this project was determining the dimensions which were derived from other models and pictures. A tad more complicated was choosing the type of masts - there were simply too many different variants. Girder masts with and without a conical concrete base or square tubes or or or... in the end I ended up with the H-profile variant shown in the picture on the upper right - not at least for pragmatic reasons.
The project almost seemed to be doomed to failure after a search lasting several weeks for suitable lenses for the lights did not give any result - until rescue emerged at RAFI. The cover cap of an indicator light from Rafi's product range exactly matched the required dimensions and optical specifications. RAFI's technical support sent me to the product manager in charge who immediately agreed to send me "20 free specimen of each colour" - Wonderful !
After the brass raw material had arrived, the question arose how to process the brass sheets being 1mm thick. Since my employer's training workshop gave up on milling in general, cutting the shields was mandated to the next water jet cutter.
After a long period of preparations I finally got started on the signals.
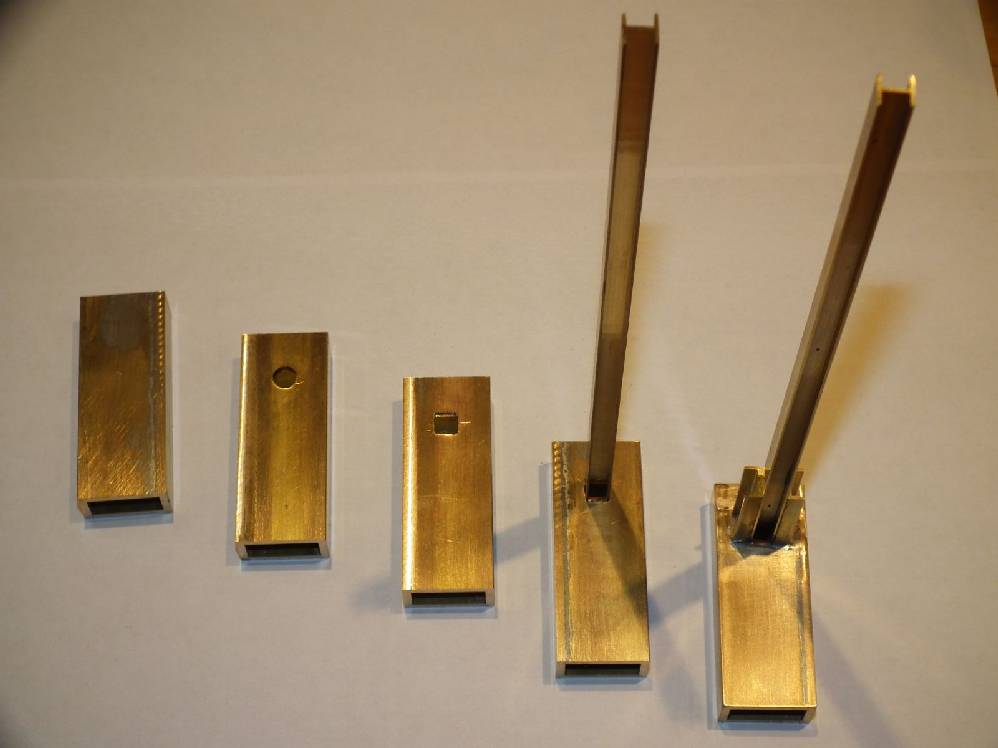
The base was soldered together from two L-shaped sections in which the mast is put in and then is supported by two U-shaped sections.
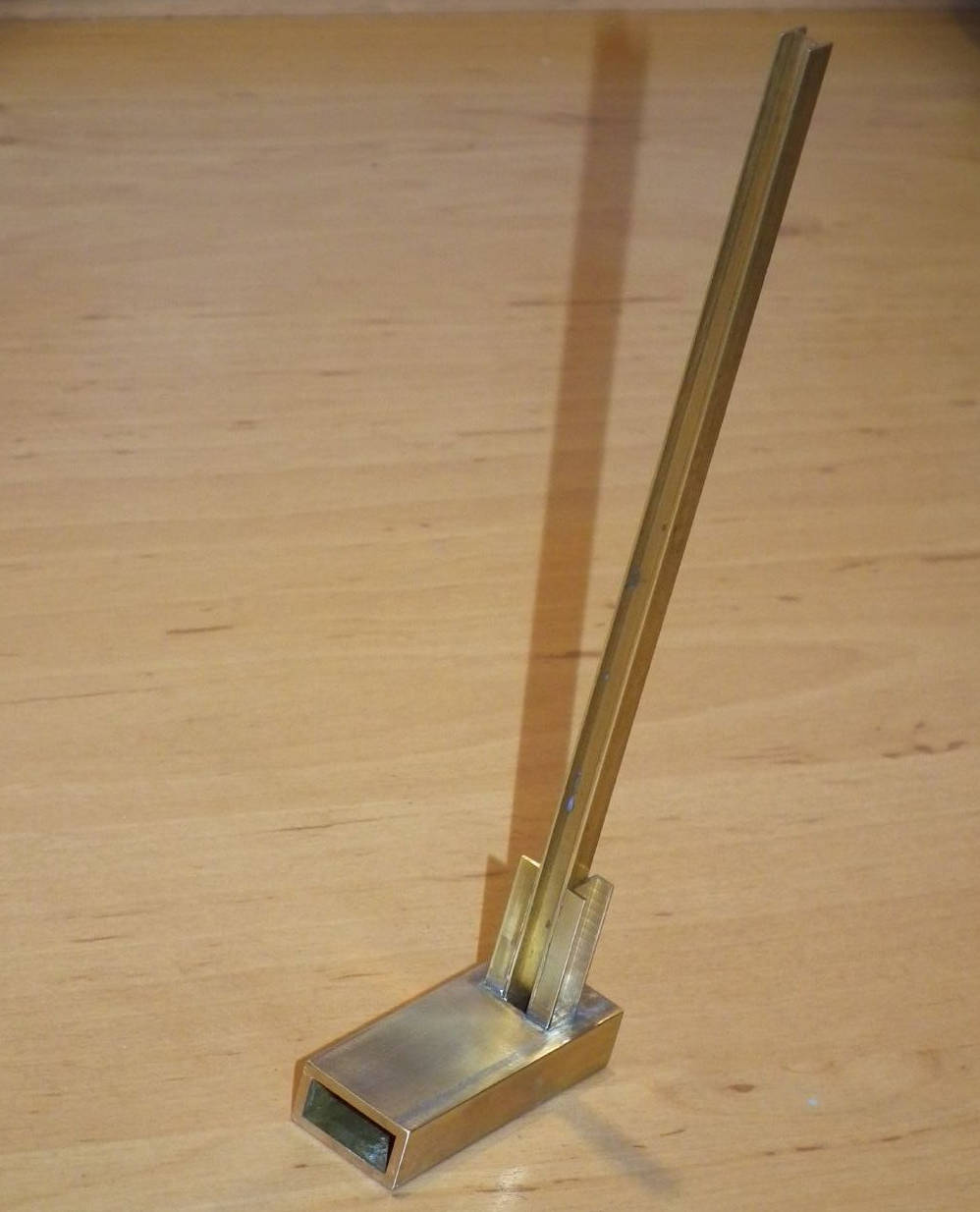
The time-consuming fettling of the solder joint requires exact filing and extensive sanding - last wet with a grit of 600.
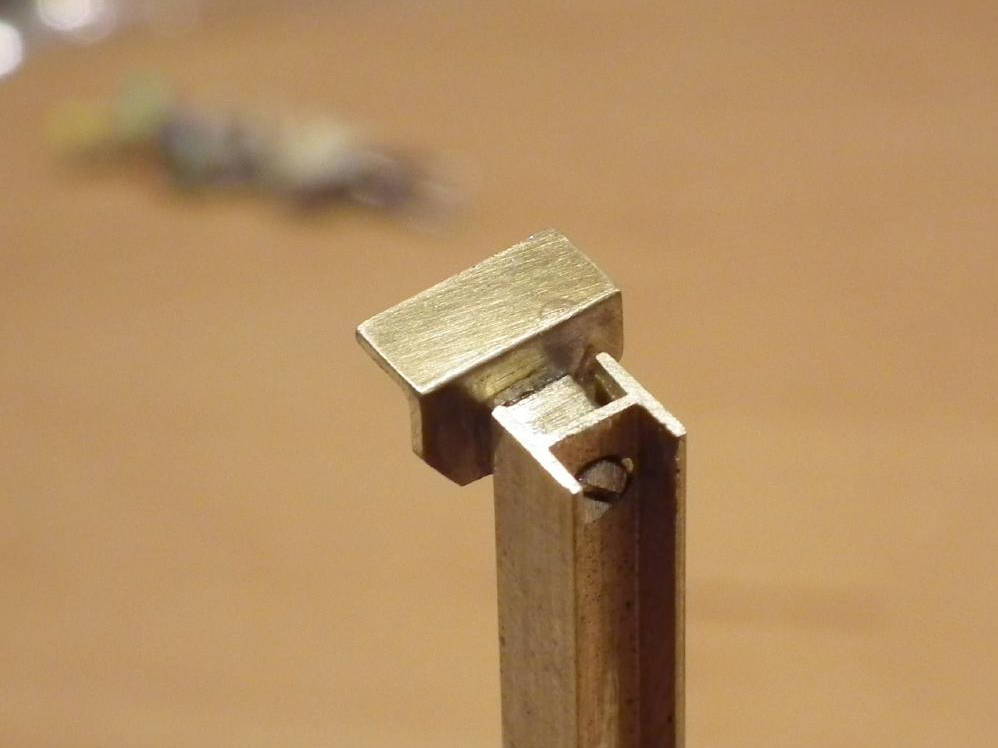
Not everything can be soldered together - especially if small parts are too near to each other stainless screws were preferred.
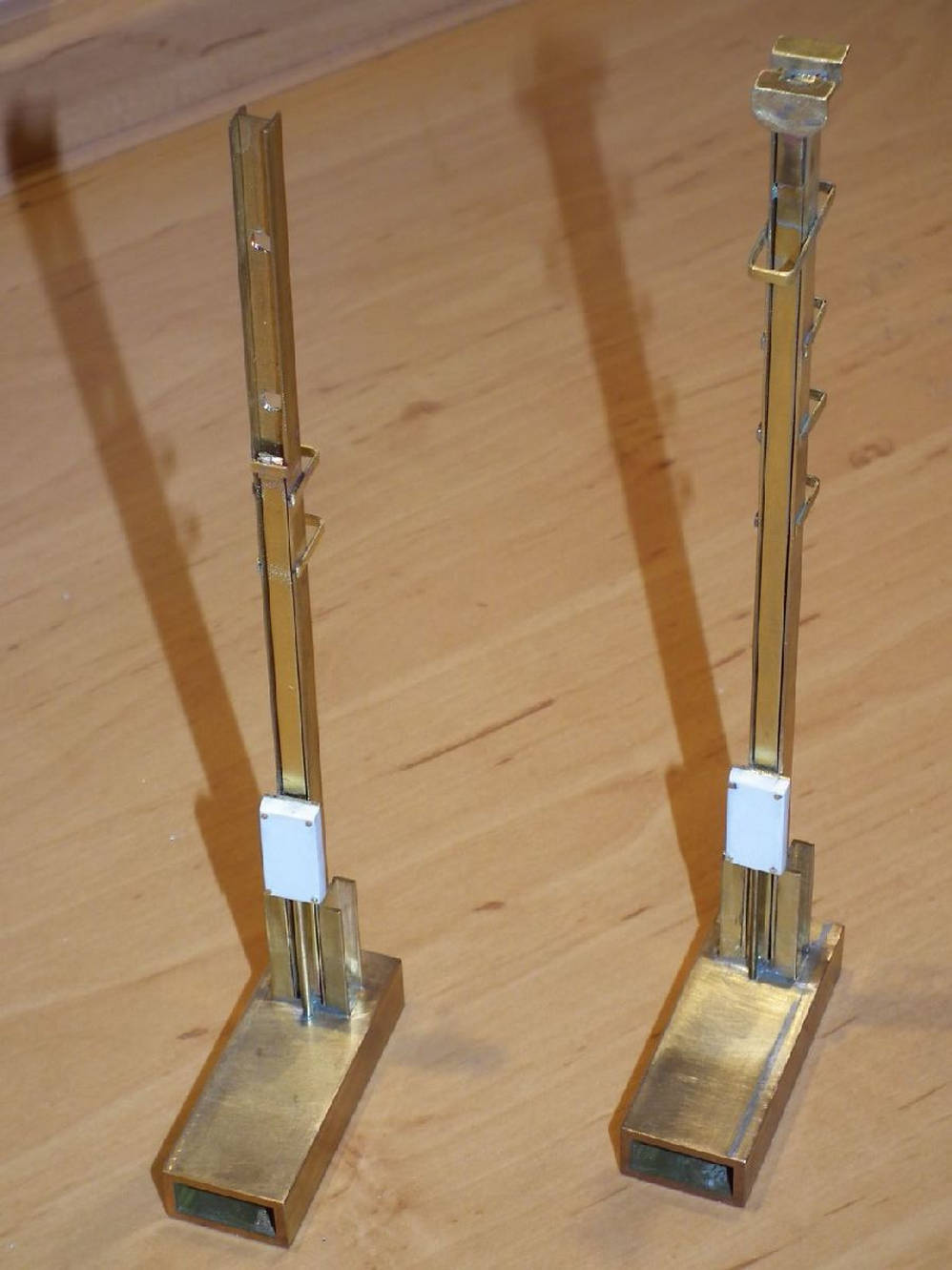
Detailing of the masts by means of steps, panellings for the wiring and junction boxes made from 2mm polystyrene.
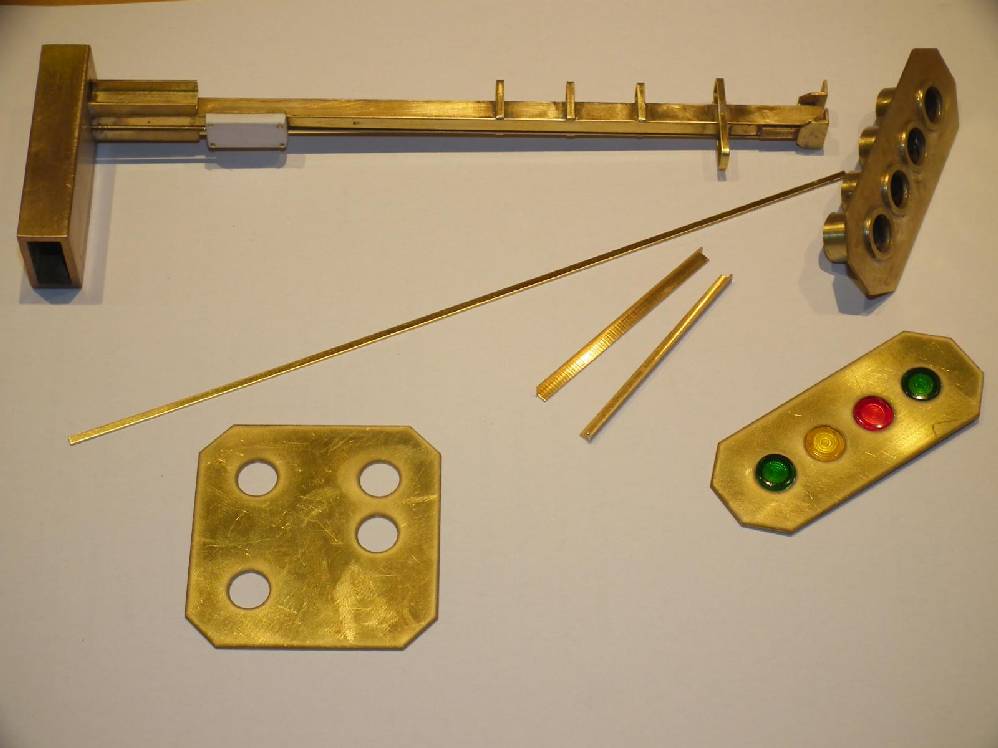
After the masts were done, the shields and lights as well as the further details in form of the baskets and rear structures were up next.
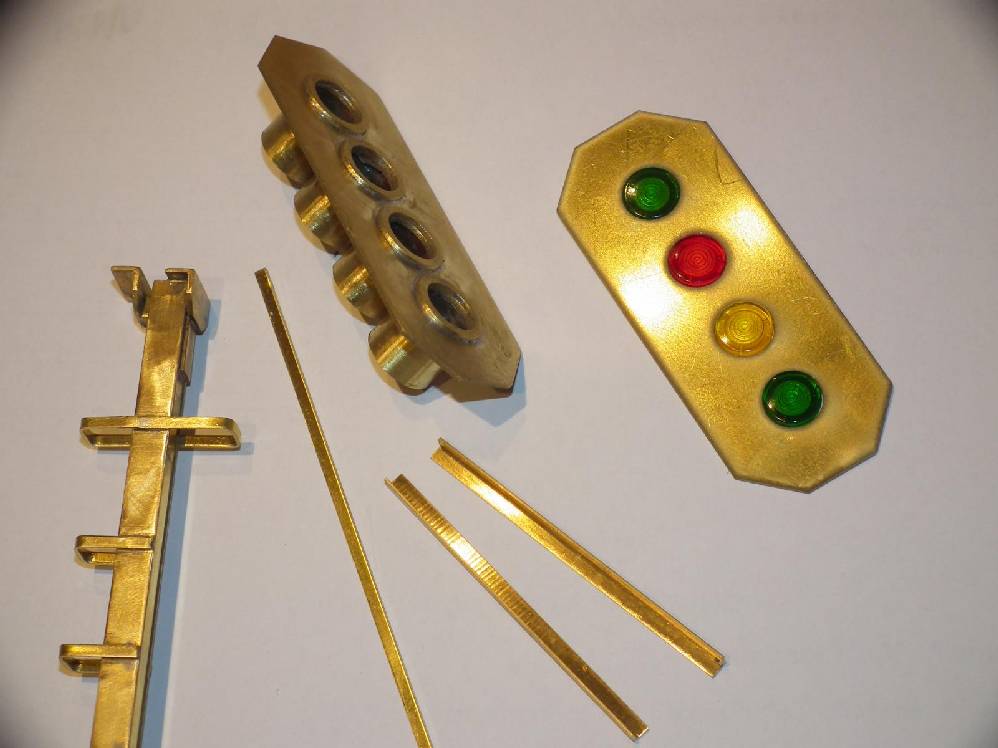
A wooden jig provided for soldering the lights' housings and rings in the correct, say centric position.
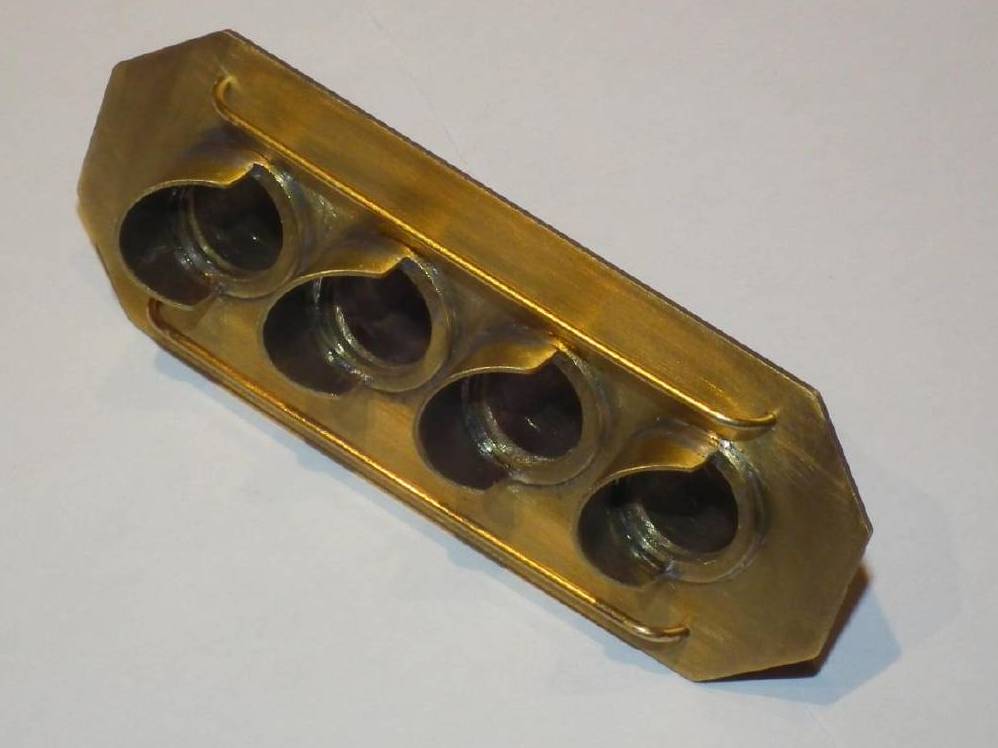
Making and applying the lense hoods required the patience of a saint as well as a surgeon's skills. The hoods were made from pieces of a 12mm brass pipe cut to length and filed to shape.
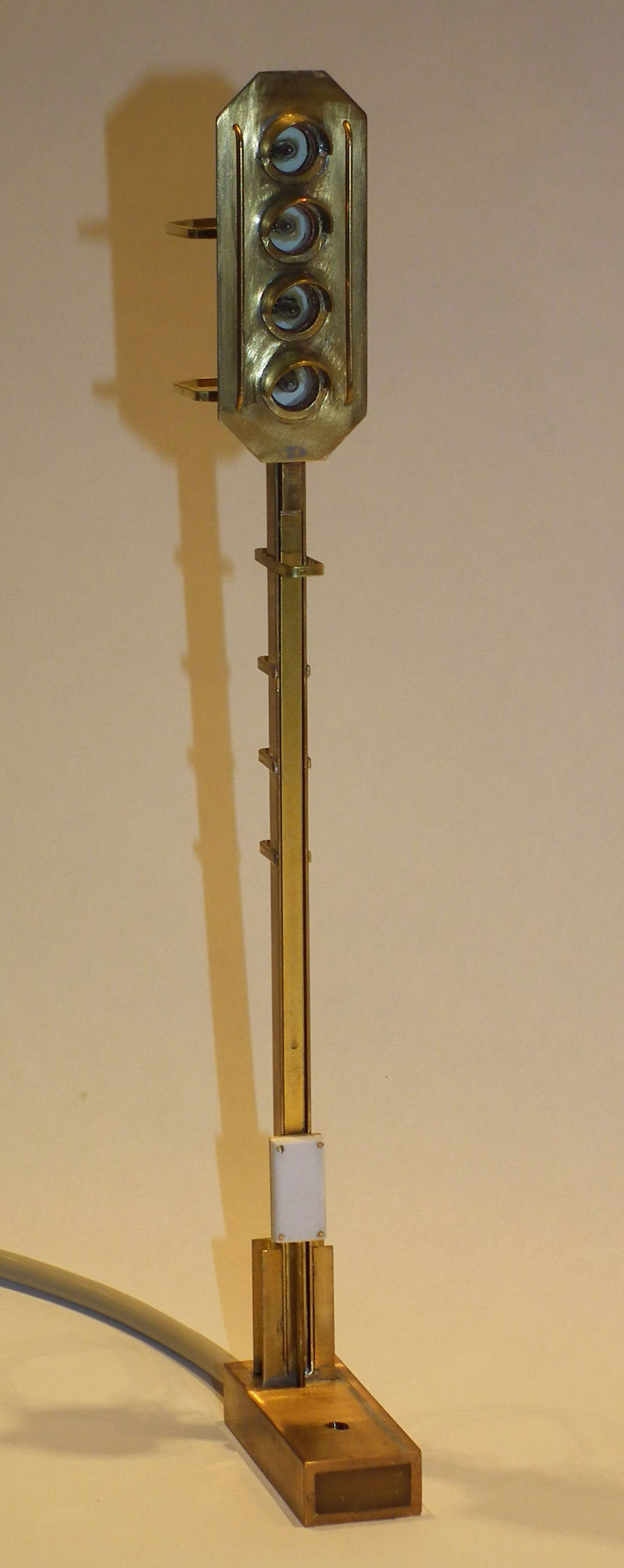
Mounting the bulbs' sockets made from two pins of a SIL IC socket and wiring them was a sort of cakewalk compared to the previous soldering and fettling work. The internal 0.8mm wire wrap cables are connected to an outdoor-capable cable inside the base. The junction box's fake screws feature a wrench size of 0.8mm...
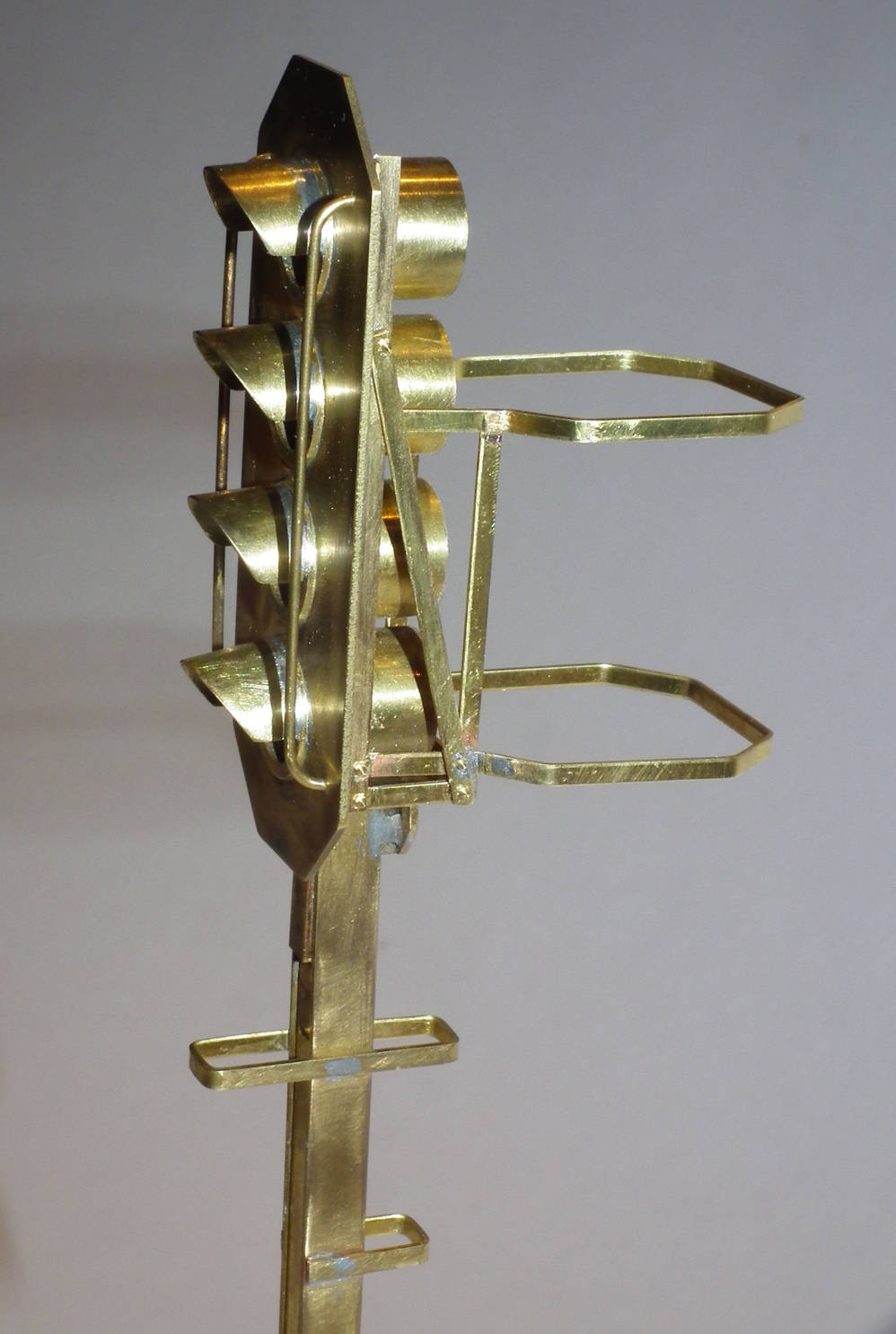
The same screws which had been used on the junction boxes were used for soldering the rods on the rear side. Holes with a diameter of 0.5mm had been drilled for inserting them before.
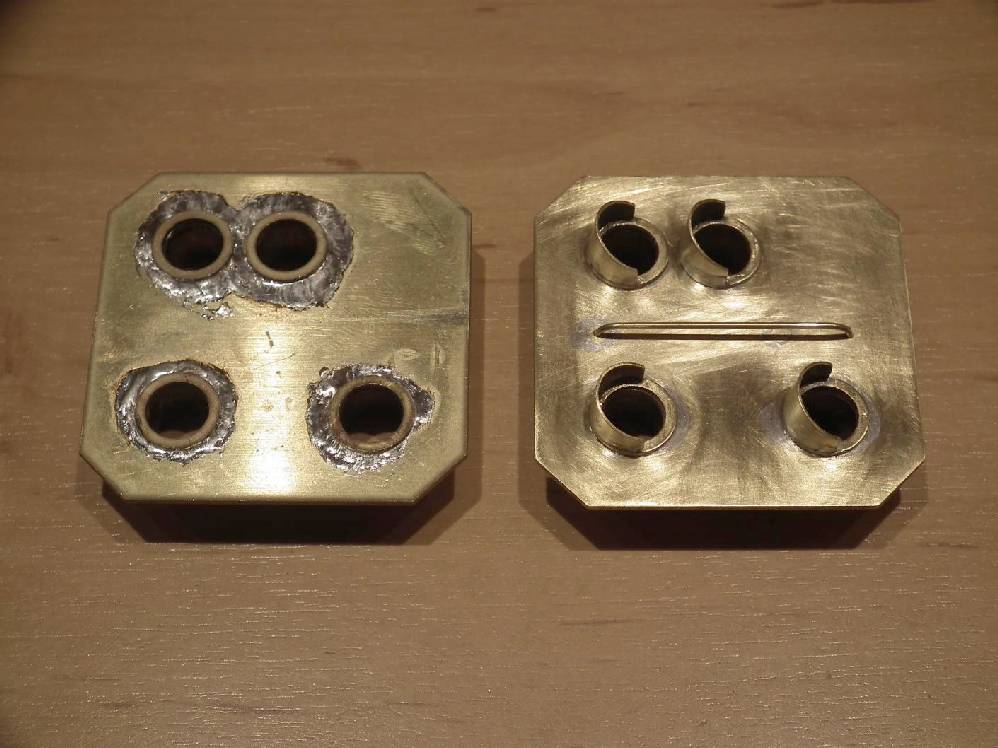
After the lights' housings made from sections of a 12mm brass pipe had been soldered to the rear side, the rings taking the lenses were soldered to the front side. After fettling the solder joints the lense hoods were soldered to the rings - which caused fettling work again, of course.
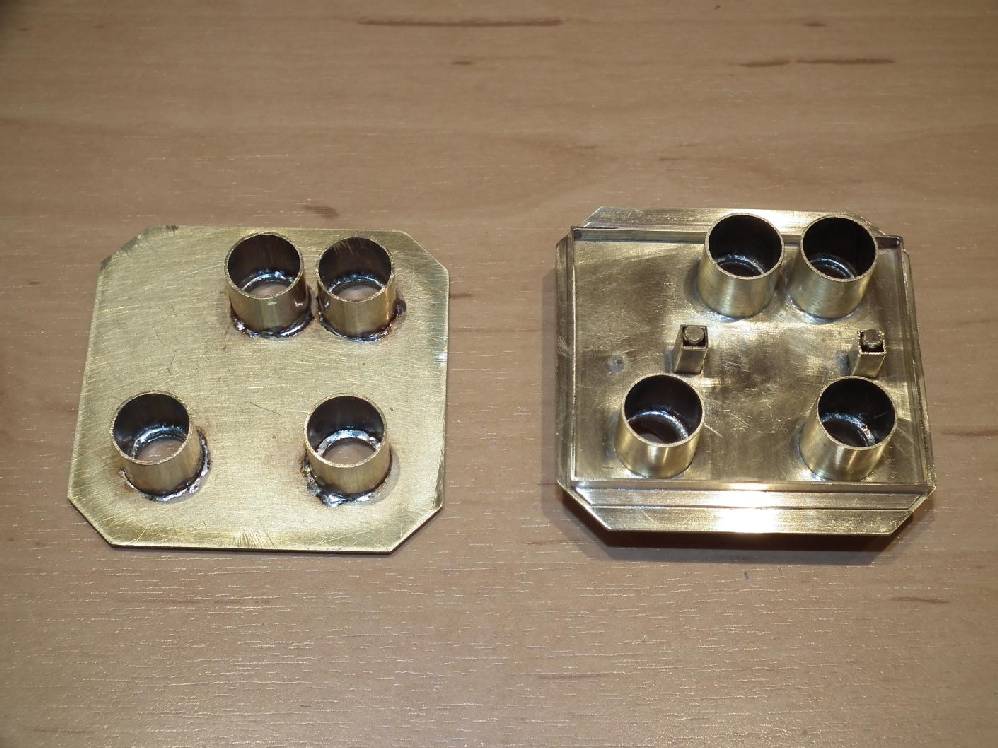
And the same imposition on the shields' rear side - but with stiffeners and mast couplings instead.
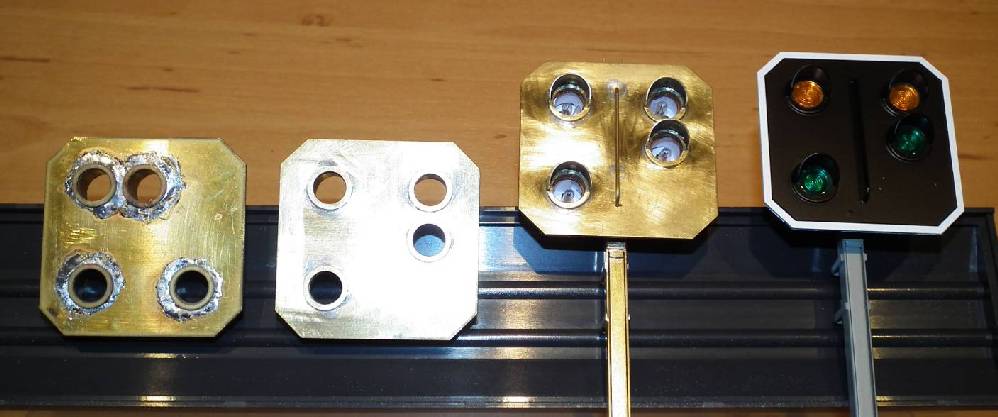
The pictures demonstrates the "genesis" from the first solder joints to the completely painted signal equipped with Fresnel lenses.
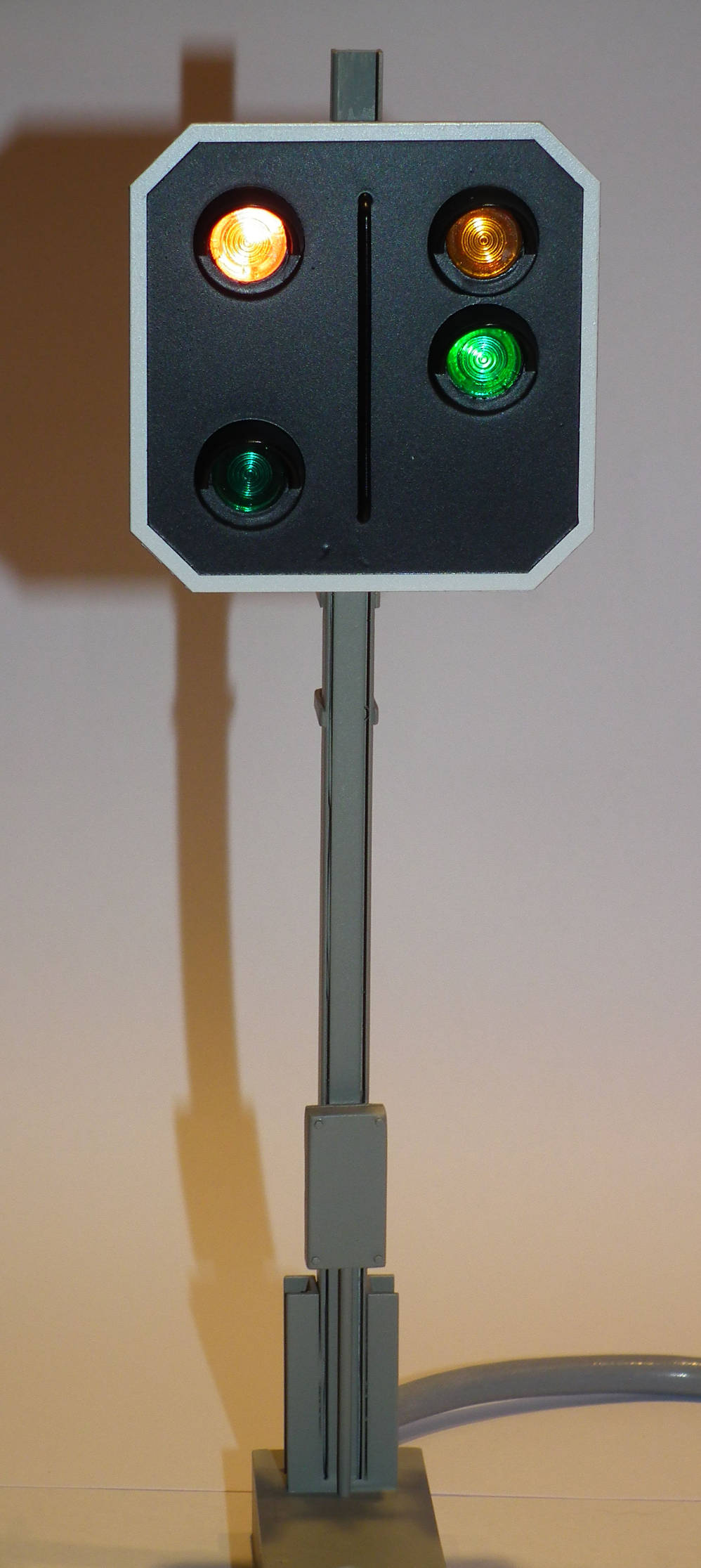
The following pictures show some detail views which almost don't adumbrate the work efforts any longer.
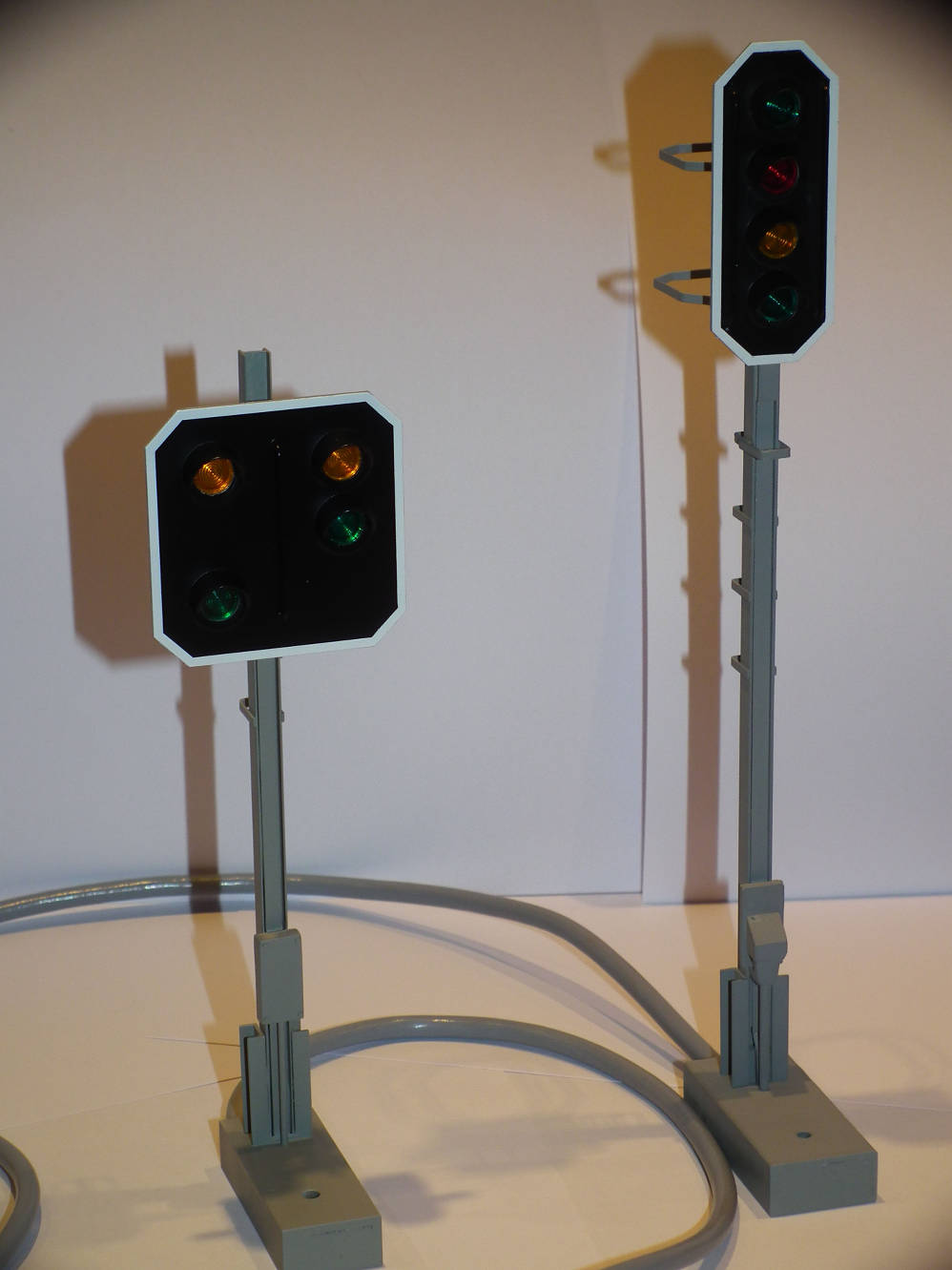
As usual the result rewards for the to some extent tremendous efforts.
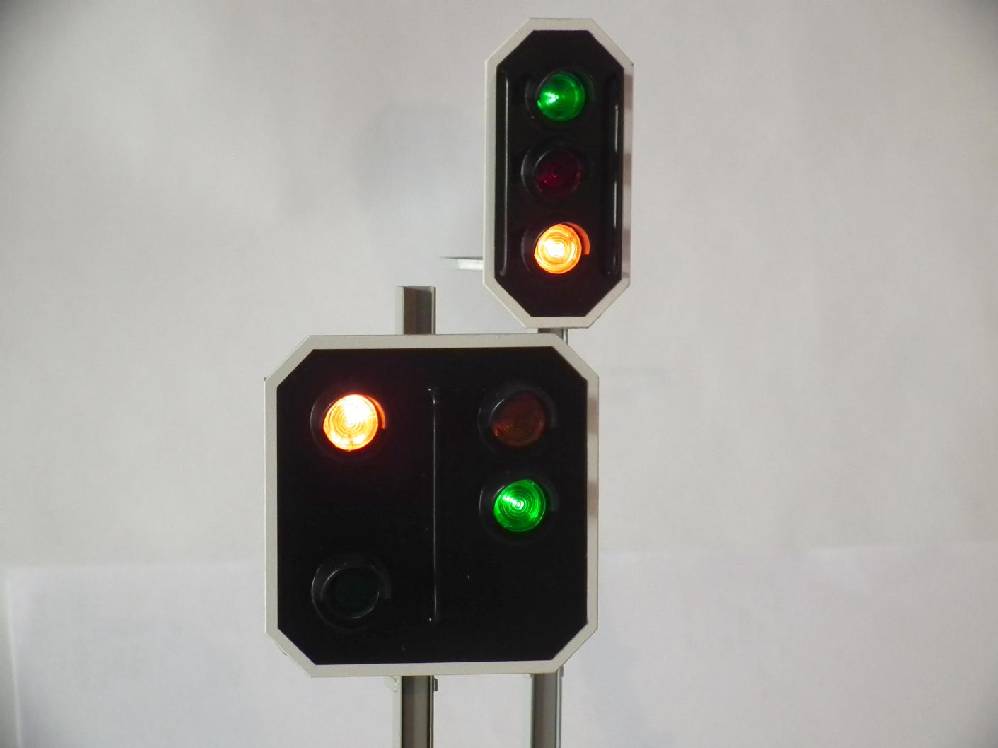
19V plug-in bulbs by Champex-Linden CL61033, made for a prototypical illumination at ~13V. Voltage in outdoor operations will be determined by either the weather station's light intensity sensor or the already existing sunrise and sundown illumination procedure.
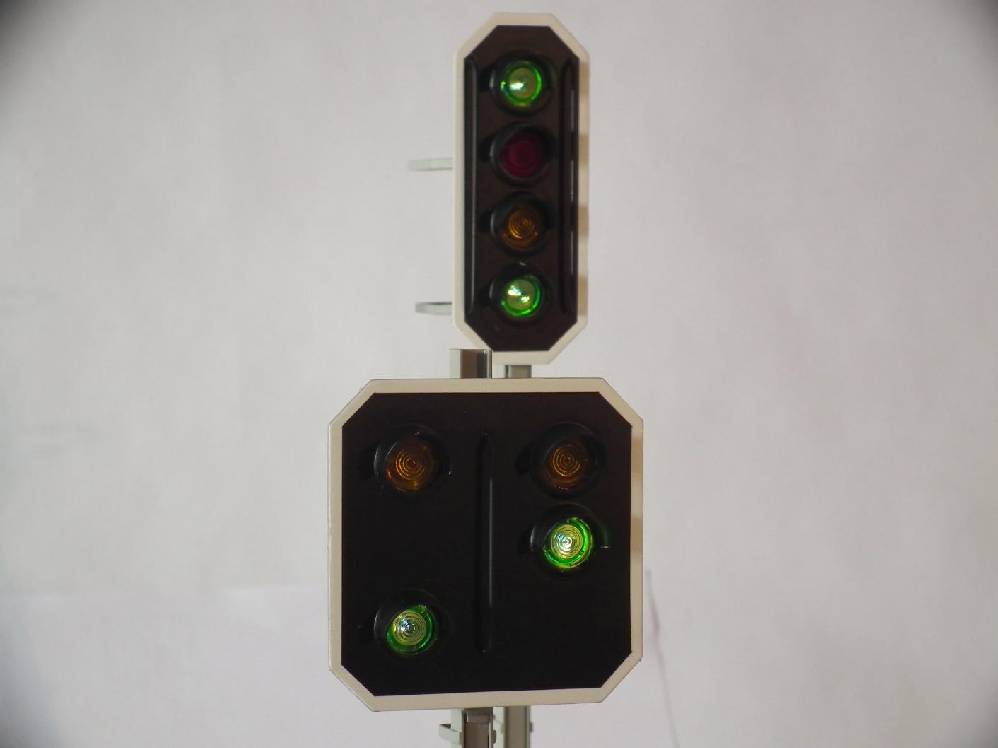
A set of a distant and a 4-light main signal
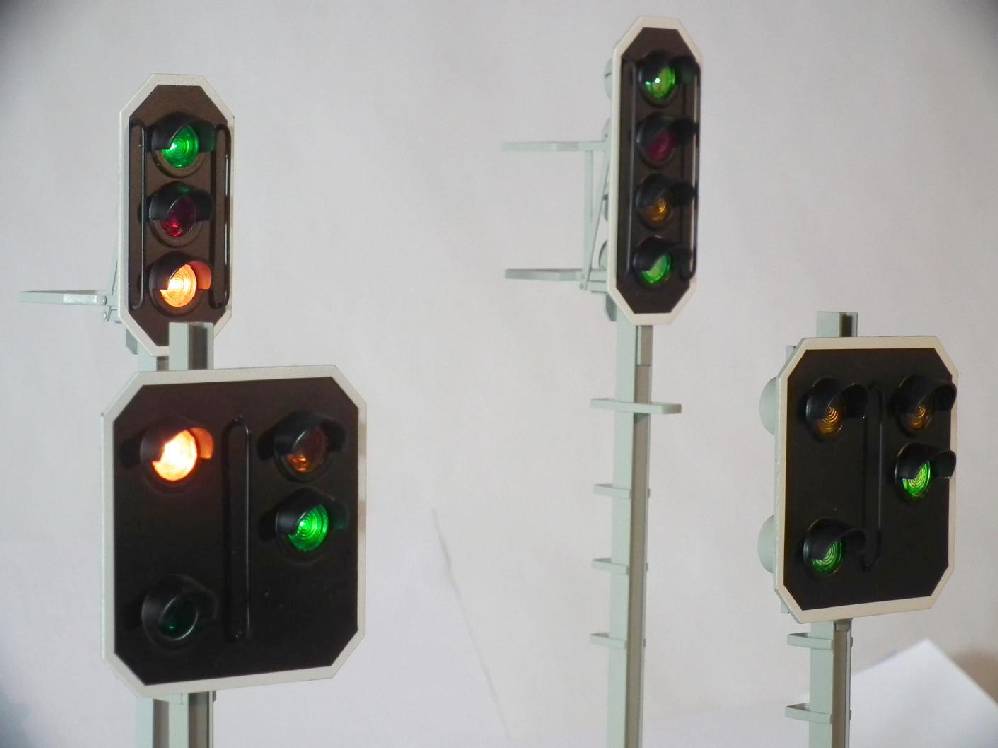
The picture shows just half the truth - all in all four distant and two 3- and 4-light signals each were made.