Katzhagen modeling department
LGB 38670 / Redesign of a RhB As 1171 "Star[c]kes Stück"
Or: Buying furniture before building the house...
I thought this coach's interior not to be very elating when it hit the road back in the year 2003 since it was prototypical in no way and so I refrained from purchasing it at that time - which was less foresightful. But now Christian Fesl's initiative to make prototypical furnishings and equipment elated me to immediately order such a set and (much to my astonishment) I found an almost unused LGB 38670 quite quickly, too.
The little project was revealed by a third party right before I was able to start the work on it and it became clear that I had to do two conversions...
The work began building a constant current power supply for the interior's new illumination matching the prototype.
The old board was removed and the new one supplies power to the new illumination's 15 LEDs.
Conversion of the ceiling lamps - bulbs out, SMD-LEDs in. Fastening with methacrylic resin.
The ceiling lamps' conversion was quite simple compared to building the spotlights from 1mm brass rods and 3mm brass tubing.
After 18 spotlights had been made for both of the cars' ceilings, they were equipped with SMD-LEDs.
A spotlight made for test purposes proves to both fit and work - 17 more were to follow.
Masked LED on a spotlight prepared for painting and the disassembled roof - its interiors aren't needed any longer.
The protoype only has two vents on the roof, hence the middle one was removed.
A polystyrene plate of 1mm is being used for the new roofliner.
Having completed the measurement, the new roofliner was cut to size and fitted into place with a suitable, i.e. sharp and robust cutter.
After the gibbings for the new roofliner had been glued in, a hot air blower puts the roofliner into its new shape.
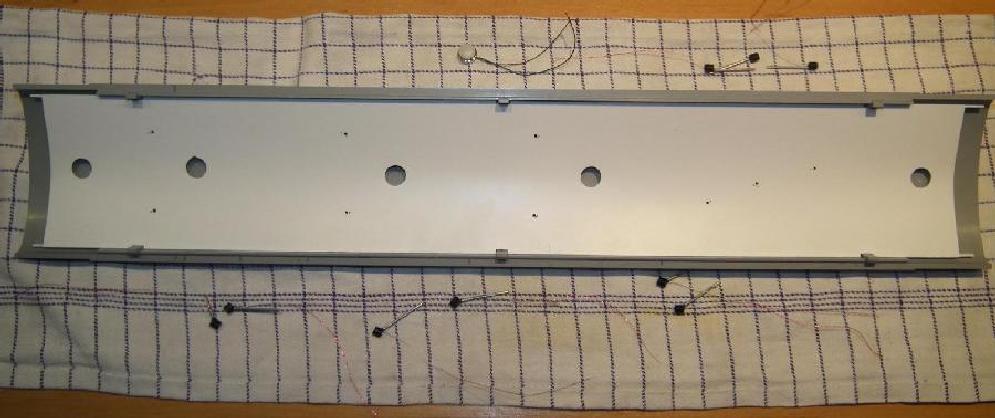
The try-on shows the treatment with the hot air blower was successful...
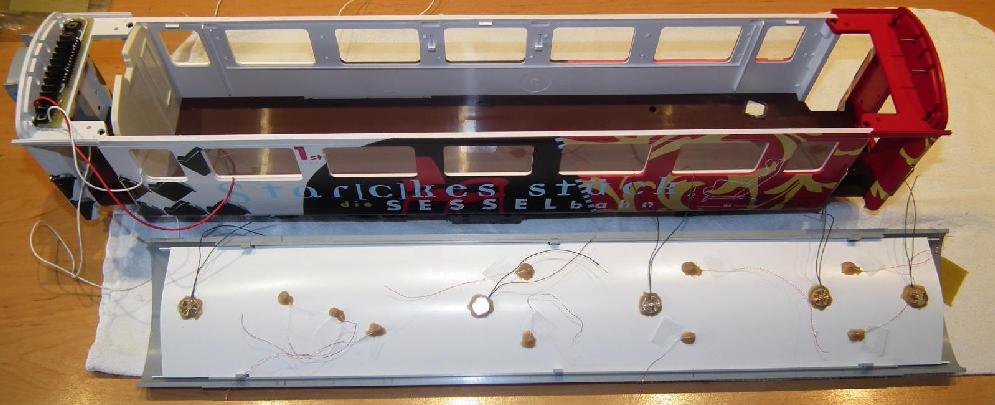
The lamps were mounted and their cables shed a light on the efforts to be expected with the wiring...

So this is no surprise - Ribbon cable for the particular plus terminals and a common ground rail.
Controlling the LEDs is done via a transistor for each of the LEDs - a first test completes successfully.
... for applying decals of the stucco and vents fakes. And then... disenchantment set in.
It turned out that numerous 3D-prints showed a severe lack of precision. Substantial rectification work was required.
Lots of filling and grinding was required for plain surfaces and the bar got prototypical railings.
The chairs required extensive sanding as well - almost every part provided for a medial dust disaster.
Plain items can be sanded easily on a table, round ones require other ideas...
All in all three rounds of sanding were required, the last one was done wet with a grit of 400 followed by a "muster".
A test of the seats shows that the furniture's proportions do fit. Thermoforming the armchairs' back rests requires a little appliance which provides for exact bending.
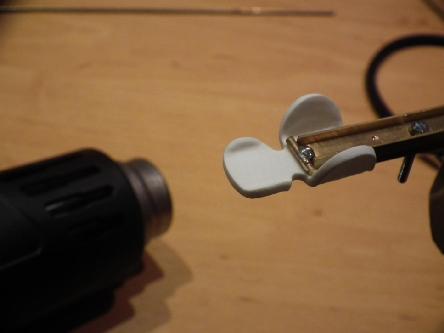
The hot air blower also was used for forming the body-contoured seats which required a little appliance for bending as well. The bar was detailed with railings and similar.
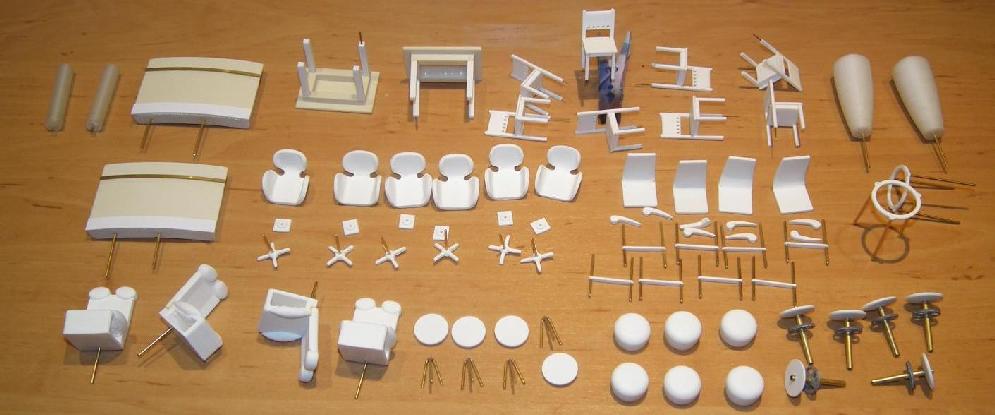
The furnishings' preassembled parts are ready to...
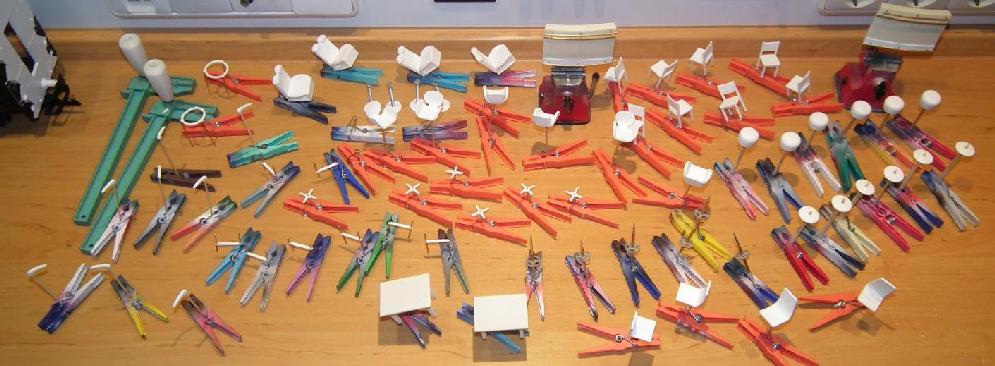
... be painted with the help of clothespins and similar.
Black parts. And brown ones. And white ones. And red ones. And...
... polystyrene boards being 1mm thick. The parts are glued to each other having fitted them into place. It's recommended to first complete the service compartment and to fit in this structure together with the divider before glueing the compartment to the divider.
After having mounted the furniture, decals and further details were applied to the interior, f.i. door frames and handles.
Nothing but fakes. The winged chairs' seat covers are made from decals which are based upon a chair's photograph. Brass flats of 1x1.5mm were used for soldering the door frame and the heating's/ventilation's gratings were made from decals based upon dotted lines produced by a word processor.
A patterned carpet instead of a simple red area in the middle of the car was a must since the RhB car put into operations in 2002 was chosen to be the model's prototype. The computer helped to quickly make a faked carpet, but it took some time to find a laser printer being able to produce a level dyeing of the gray colour. The chessboard was easy to establish - thanks to a pre-cut and a transfer film.
In- and exterior view of the service compartment and the divider before assembling and installing them.
The furniture was installed after having mounted the service compartment and the dividers.
All pieces of furniture were anchored to the floor using 0.5, 1.0 or 1.5mm brass rods and methacrylic resin.
Despite the numerous elements are quite different regarding their shapes and colours, the coach gives a very pleasing impression.
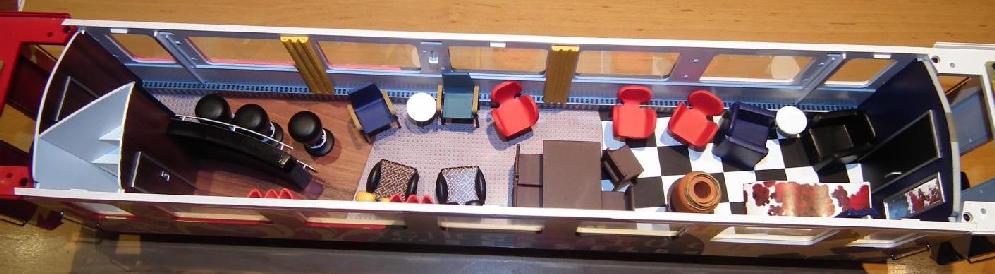
A kind soul who once had rented this car provided numerous pictures which were of great help with positioning the furniture - Many thanks to Ernst !
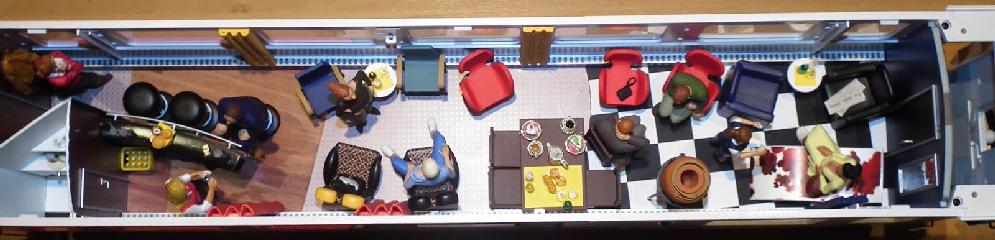
Details like tableware, glasses and bottles were provided by various manufacturers - see the related hints at the bottom of this page.
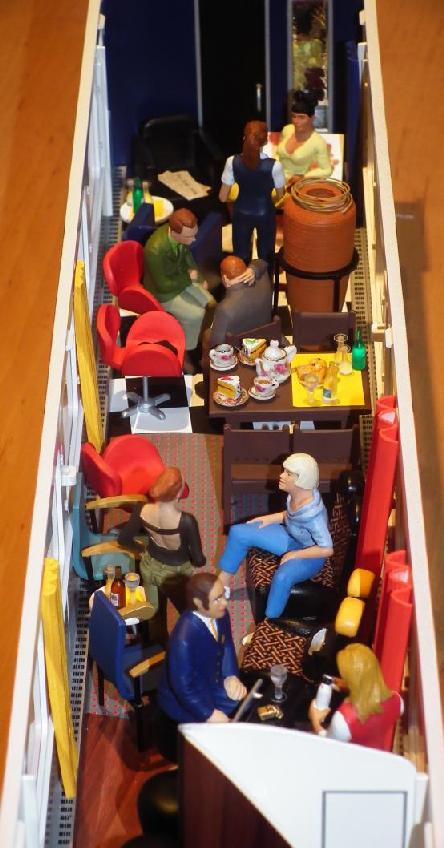
Closer looks into the car from opposite directions tell there is a wide variety of details there.
The following picture show more....
The different design elements reflect everyday situations not necessarily having to do with railways...
... and provide for the car's very own and special charm to which the furniture's design does add quite significantly.
Both the bar and the suite next to it do look inviting.
Exact masking of the buffer beams - for the last painting activity with this project - was achieved using small strips of an extreme flexible adhesive film. The parts for the second car are ready for assembly...

Done ! Having worked a tad more than six weeks on the conversions, the cars were successfully put into a more prototypical shape.
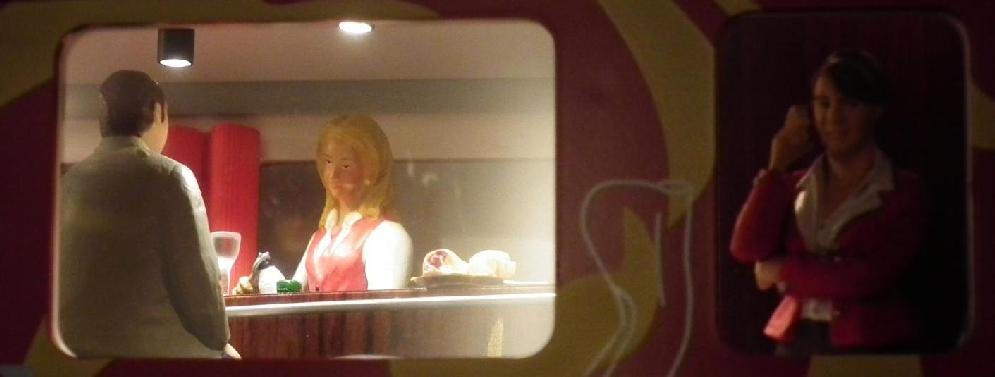
Items | Manufacturer/Provider |
---|---|
Furnishing | Christian Fesl |
Passengers | Preiser |
Staff | Prehm |
Brass wrought material | Fiedler |
Plastic boards | Modulor |
Glassware/Bottles | DS Modellbau |
Porcelain | Small Dreams |
Downloads | |
---|---|
For white adhesive film | Divan bed and door frame service compartment |
Carpet for new coach | |
For white decal film | Seat cover winged chair |
For clear decal film | Heating/ventilation gratings |
Ceiling decorations |