Katzhagen - Archive - May 2010
A RhB flat car with stakes - Building a Rp-w
As such a car, which was announced by LGB several years ago, never hit the road (yet) and because my corn vessels needed a suitable lift, I decided to make use of a related offer by Hans-Peter Langula. HPL provided both the numerous small parts for detailing the model and the instructions which were published in the "Gartenbahn-Profi" magazine.Off we go...
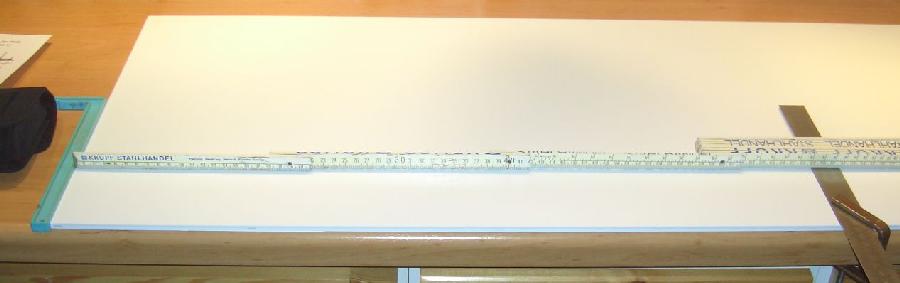
Completely new dimensions for the term panalized structure. Cutting polystyrene plates to size for the chassis.
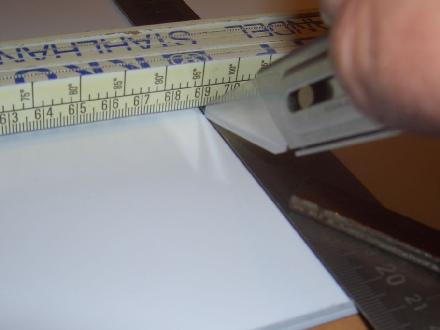
Carving and breaking - a job for a glazier.
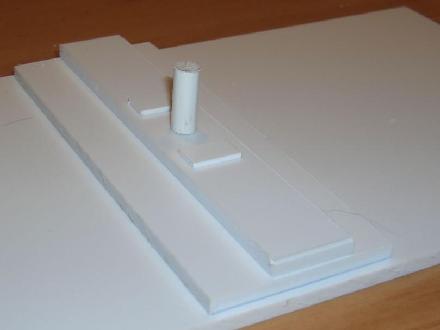
Parts for one of the truck's mounting point.
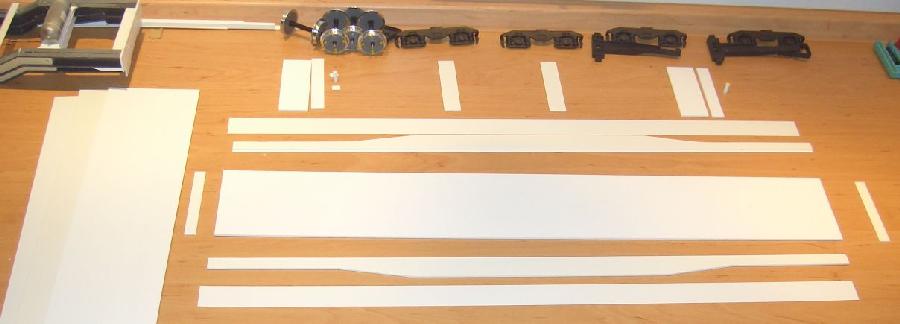
Prefabricated parts for the chassis and the trucks.
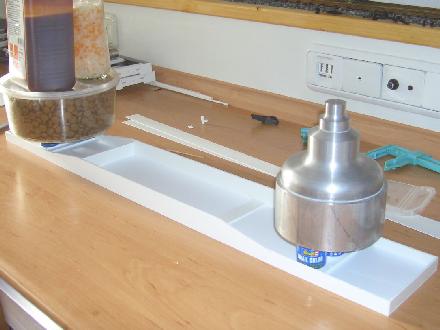
Cementing the trucks' mounting points below the preassembled chassis.
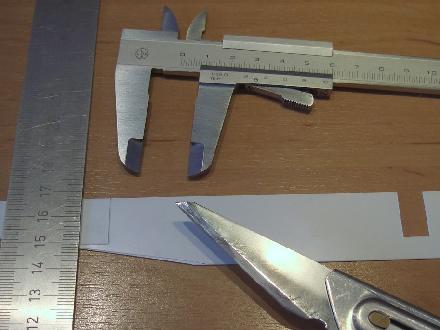
Cutting out the recesses for the stanchion sockets.
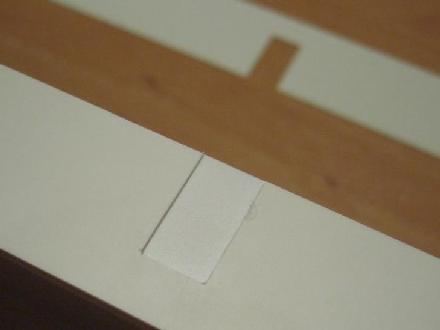
The recesses are used as a mounting aid for the stanchion sockets.
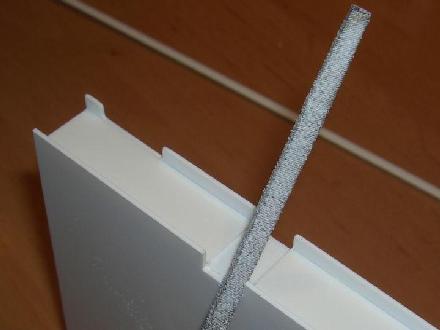
Adjusting the frame's parts to the recesses.
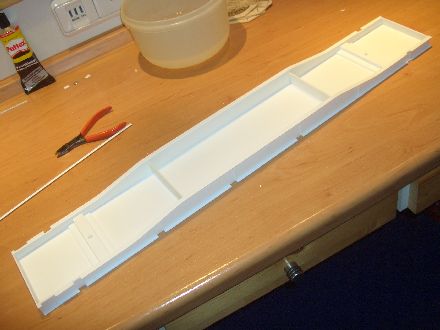
Preassembled Chassis with recesses for the stanchion sockets.
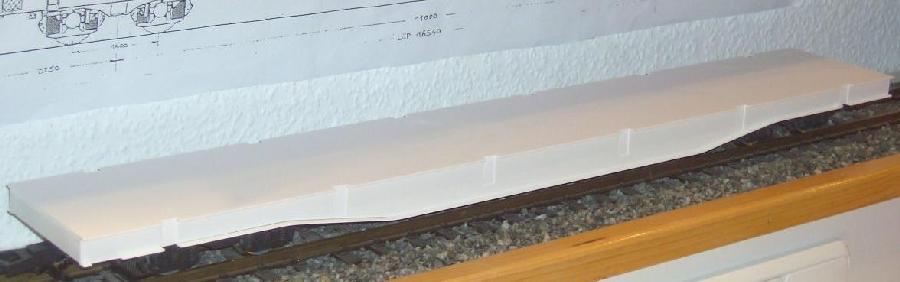
The assembly passed a first vague test. With a platform length of 69cm and a length between buffers of 73.3cm (real 1:22.5) this one is a quite long car.
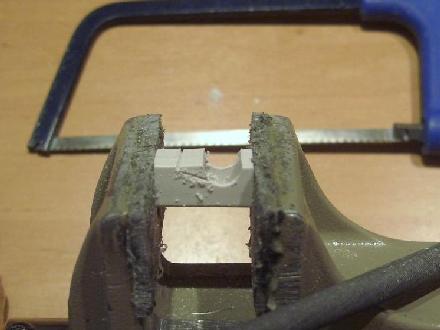
Making of the stanchion sockets - using a file and a saw.
Deviations from the instruction
are necessary for the truck mounting points and in case one neither posseses a milling machine for the stanchion socket's recesses nor a standing drill for machining the stanchion sockets themselves ...
Without thickening the truck mounting points by 3mm (my choice) or reducing the buffer beams' height, the drawbars won't fit below the buffer beams.
The frame sides were composed of three instead of two layers and the recesses were applied to a 0.5mm polystyrene plate as shown above. Accordingly, one of the other plates was choosen 0.5mm thinner.
Processing the stanchion sockets was done manually with a 7.5mm round file instead of a standing drill with a suitable holding appliance.
are necessary for the truck mounting points and in case one neither posseses a milling machine for the stanchion socket's recesses nor a standing drill for machining the stanchion sockets themselves ...
Without thickening the truck mounting points by 3mm (my choice) or reducing the buffer beams' height, the drawbars won't fit below the buffer beams.
The frame sides were composed of three instead of two layers and the recesses were applied to a 0.5mm polystyrene plate as shown above. Accordingly, one of the other plates was choosen 0.5mm thinner.
Processing the stanchion sockets was done manually with a 7.5mm round file instead of a standing drill with a suitable holding appliance.
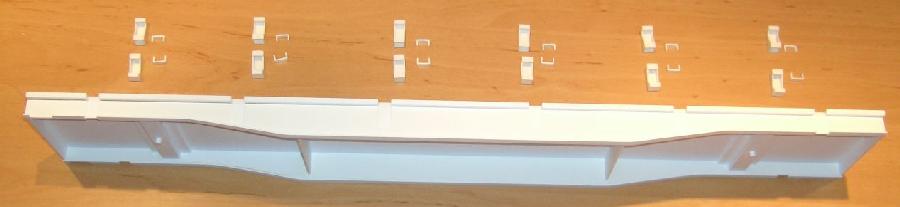
Twelve stanchion sockets with fortification collars prepared to be mounted on the preassembled chassis.
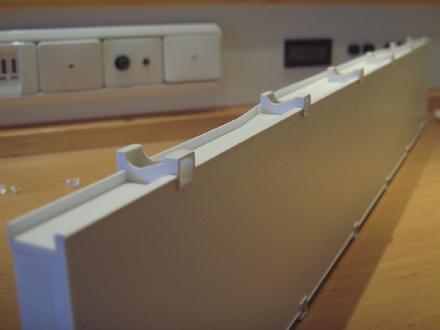
The stanchion sockets are mounted, the collars are up next.
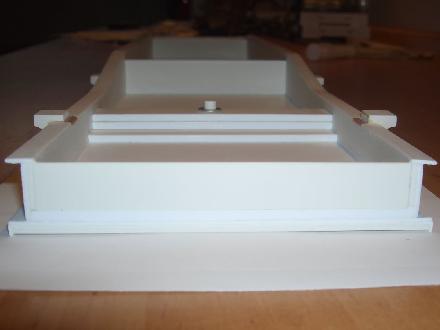
This view illustrates the assembly's polystyrene plate layers.
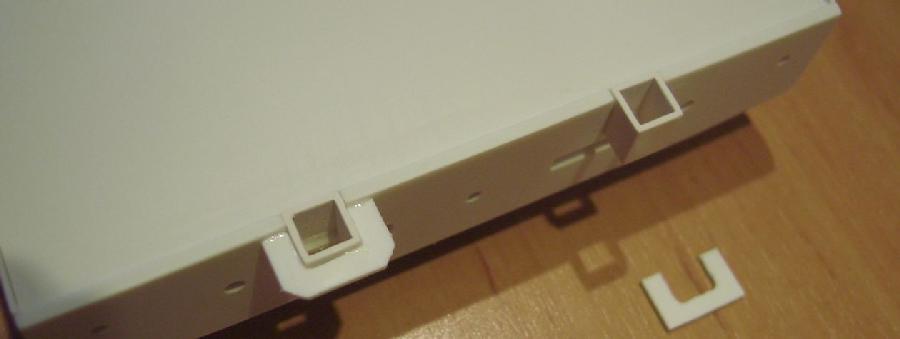
After making the buffer beams, they are populated with numerous details such as the parking brake's transmission, lugs and compressed-air lines.
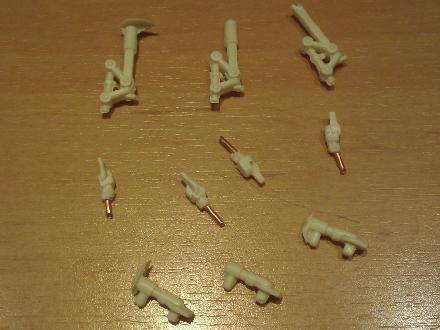
Coupler parts, hose couplings and a further part of the compressed-air system.
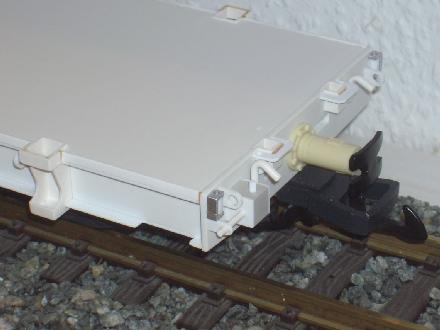
The buffer beam - almost completely equipped. Just the coupler parts are missing.
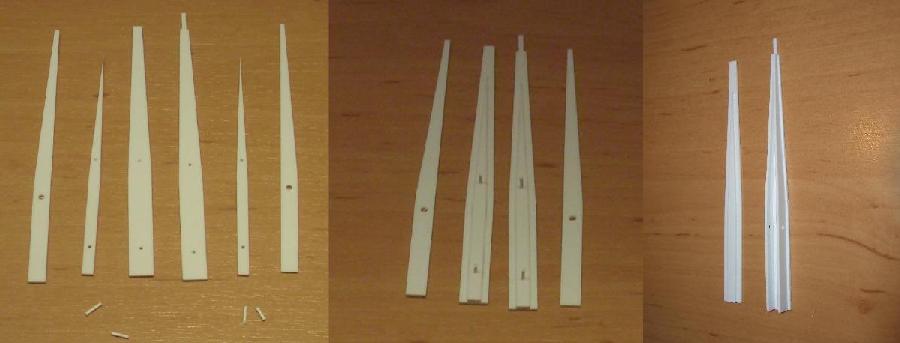
A stanchion is made from four side parts and two guiding parts as well as four centering pins. Finally, both of the parts on the right are joined together.
Aril 2010 | Archive "Current Affairs" | June 2010