Katzhagen - Archive - July 2010
A RhB flat car with stakes - Completion and commissioning
Only a few jobs with detailing and varnishing the model were pending now. Unknown terretory was entered with hot deformation of polystyrene at the stanchions' upper ends. The latter were bent around a soldering iron's thin round tip at a temperature of 150° Celsius and so formed to lugs.Apart from making up a few additional small parts, simple holding appliances were needed for varnishing all of the small parts.
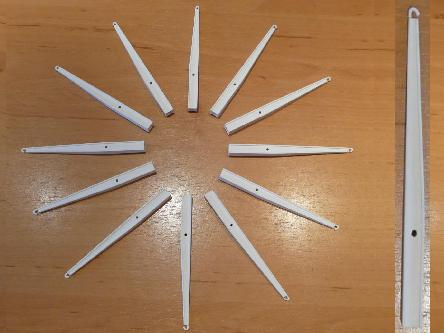
Stanchions ready to be varnished - now with the lugs at their upper ends.
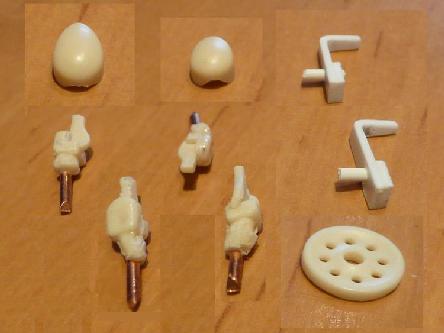
Parts of the pneumatic and brake system. Cast or "carved".
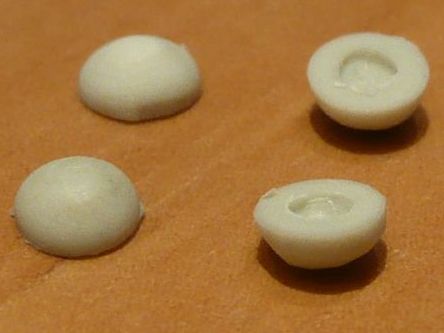
Caps - made from a 3mm polystyrene rod.
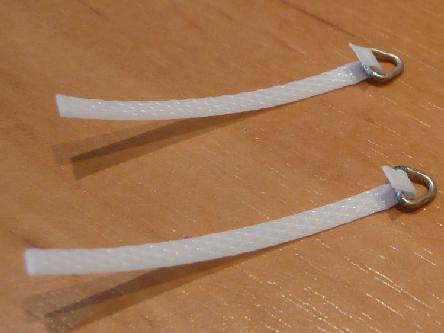
Belt dummies - made from plastic tape and soldered silver wire.
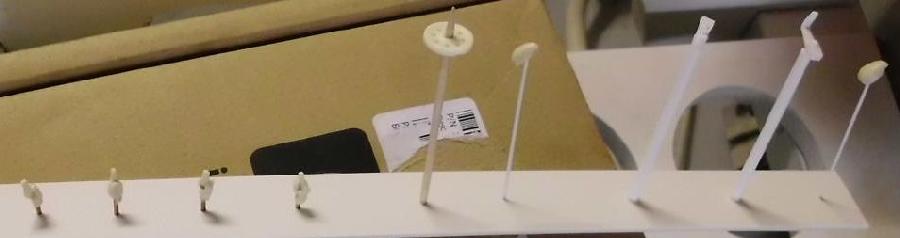
A simple fixture for varnishing those parts which had to be coloured red. The smallest parts were fixed with a little drop of contact adhesive.
Varnishing
with an airbrush gun definitely is not one of my favourite tasks, since both the related preparations and the post job tasks are quite time-consuming. Fortunately, the results are worth these efforts.Once again it turned out, that making use of colours from the known model manufacturers was a good decision. Processing is much easier and the results are much better than with products from a DIY store. Viscosity and pigmentation differ quite a lot.
As a marginal note: The airbrush equipment is still fully functional after more than 20 years - I used it first in 1988 to colour a robbe "Happy Hunter".

Kebab spits and a carton - varnishing the stanchions.
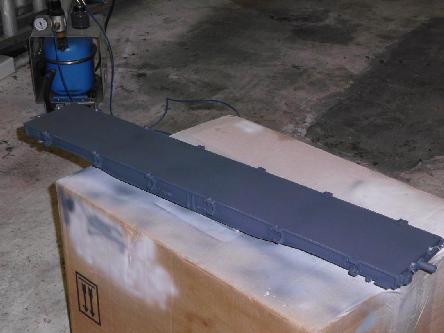
According to the RhB's colourtable this ought to be "zinc dust". RAL values ?
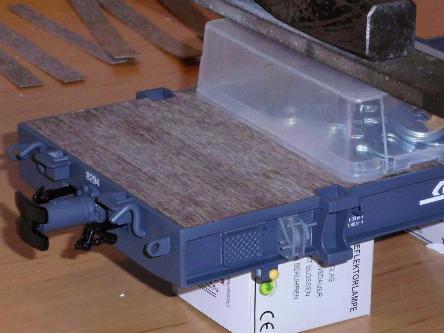
Planking the load area with a wood counterfeit - a Formica plate's back.
After finishing the paint work, the belt dummies were made from plastic tape
(the stuff which is used to keep cardboard boxes shut) and from silver wire
wich was bent to shape and finally soldered (see picture above). One end of
the tape was bent to a loop for the lug and fixed with a drop of cyanoacrylate
adhesive.
A baffling detailed representation of the load area's wooden structure was achieved using a plate of Formica. A safety guillotine was used to cut the plate into suitable stripes which then were glued with their face upside down to the car's surface. Since Formica is a subject to torsion, some load is necessary until the adhesive's hardening is complete. Otherwise one may need to repeat the glueing - and perhaps will mess up the paint work then...
A baffling detailed representation of the load area's wooden structure was achieved using a plate of Formica. A safety guillotine was used to cut the plate into suitable stripes which then were glued with their face upside down to the car's surface. Since Formica is a subject to torsion, some load is necessary until the adhesive's hardening is complete. Otherwise one may need to repeat the glueing - and perhaps will mess up the paint work then...
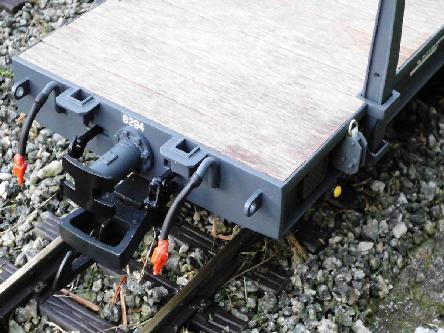
Everything has an end, but the Rp-W has two - One buffer beam's details ...
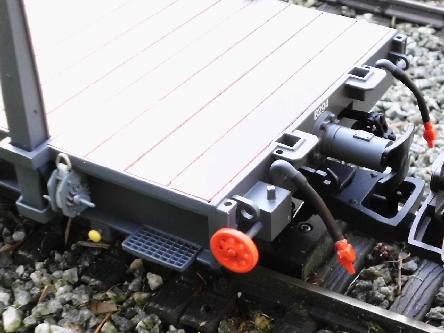
... and those of the other one.
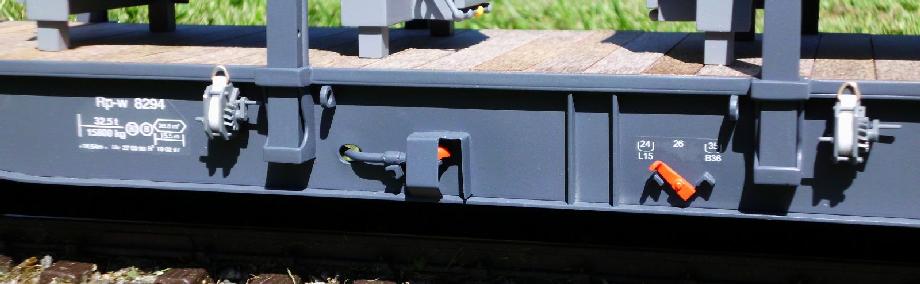
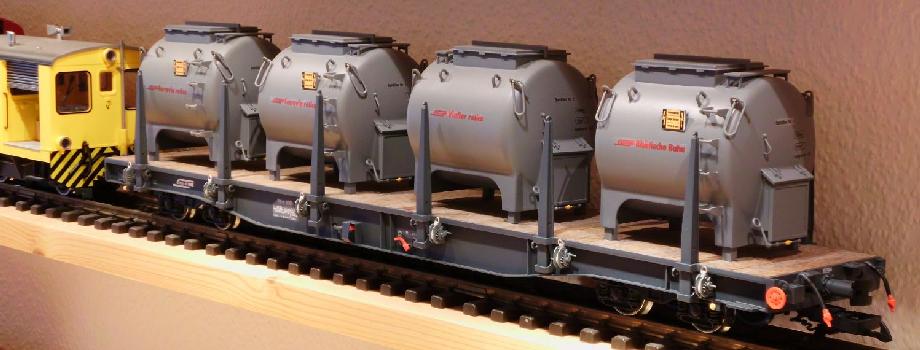
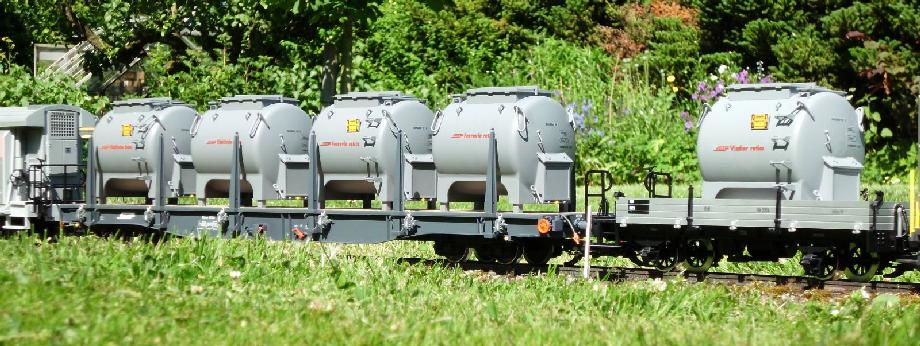
And what's up next ? A Sb-K !
June 2010 | Archive "Current Affairs" | August 2010